Lean making method for Goodyear seam shoes
A manufacturing method, Goodyear's technology, applied in the field of shoe sewing, to achieve the effect of reducing material cost, reducing material damage, and improving quality
- Summary
- Abstract
- Description
- Claims
- Application Information
AI Technical Summary
Problems solved by technology
Method used
Image
Examples
Embodiment Construction
[0033] The following will clearly and completely describe the technical solutions in the embodiments of the present invention in conjunction with the embodiments of the present invention. Obviously, the described embodiments are only a part of the embodiments of the present invention, rather than all the embodiments. Based on the embodiments of the present invention, all other embodiments obtained by those of ordinary skill in the art without creative work shall fall within the protection scope of the present invention.
[0034] A lean manufacturing method for Goodyear stitched shoes: First, prepare the required upper 1, welt 2, midsole 3, filling layer 4 and outsole 5, such as figure 1 As shown; then, use a special sewing machine 7 to directly sew the shaped upper 1 with the welt 2 and the midsole 3 into a whole (the traditional crafts are: first clamp, pull nails, sew the inner welt, and cut the upper foot , Sanding, bottom bonding), such as figure 2 As shown; secondly, put the...
PUM
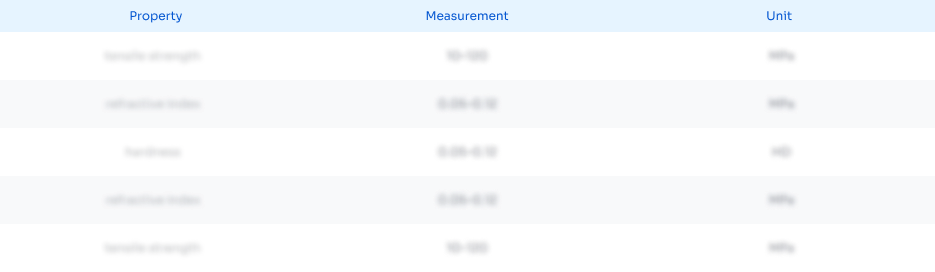
Abstract
Description
Claims
Application Information

- R&D
- Intellectual Property
- Life Sciences
- Materials
- Tech Scout
- Unparalleled Data Quality
- Higher Quality Content
- 60% Fewer Hallucinations
Browse by: Latest US Patents, China's latest patents, Technical Efficacy Thesaurus, Application Domain, Technology Topic, Popular Technical Reports.
© 2025 PatSnap. All rights reserved.Legal|Privacy policy|Modern Slavery Act Transparency Statement|Sitemap|About US| Contact US: help@patsnap.com