Low resistance hydraulic cavitation structure with microchannel heat exchange enhancing function
A technology of hydraulic structure and hydraulic cavitation, used in heat exchange equipment, lighting and heating equipment, lasers, etc., can solve the problems of increasing pump power and large flow resistance in heat transfer performance, reducing pump power input and reducing flow resistance. Loss, the effect of enhancing the heat transfer effect
- Summary
- Abstract
- Description
- Claims
- Application Information
AI Technical Summary
Problems solved by technology
Method used
Image
Examples
Embodiment Construction
[0020] The following is attached figure 1 ~4 describes specific embodiments of the present invention.
[0021] Such as figure 1 and Figure 2a , Figure 2b As shown, the low-resistance hydraulic cavitation structure for strengthening microchannel heat exchange described in the present invention includes: a base plate 1, a cooling microchannel 2, a microchannel inlet flow distribution chamber 3, a microchannel outlet liquid collection chamber 4, and an induced cavity The phenomenon of hydrodynamic structure5.
[0022] A plurality of cooling microchannels 2 are uniformly and parallelly arranged on the base plate 1. One end of the cooling microchannel is a fluid inlet, and the other end is a fluid outlet. The fluid inlet is provided with a flow distribution chamber 3, and the fluid outlet is provided with a liquid collection chamber 4. Each cooling microchannel 2 between the flow distribution chamber 3 and the liquid collection chamber 4 is provided with a tapered-divergent h...
PUM
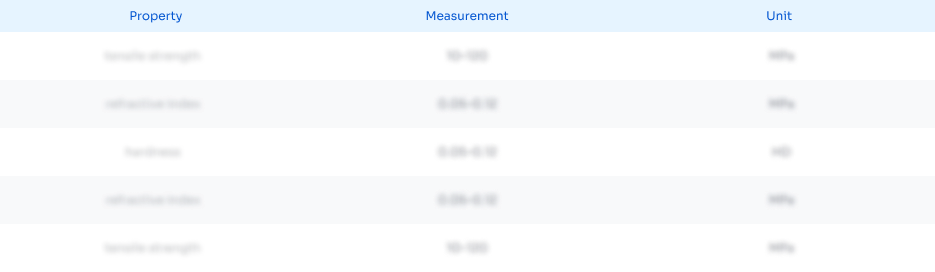
Abstract
Description
Claims
Application Information

- R&D
- Intellectual Property
- Life Sciences
- Materials
- Tech Scout
- Unparalleled Data Quality
- Higher Quality Content
- 60% Fewer Hallucinations
Browse by: Latest US Patents, China's latest patents, Technical Efficacy Thesaurus, Application Domain, Technology Topic, Popular Technical Reports.
© 2025 PatSnap. All rights reserved.Legal|Privacy policy|Modern Slavery Act Transparency Statement|Sitemap|About US| Contact US: help@patsnap.com