Modal woven fabric splitting process
A process and fabric technology, applied in the field of modal woven fabric opening technology, can solve the problems of poor opening effect and uniformity, hard cloth surface, and unclean removal of hairiness on the cloth surface. The effect of simple and easy process
- Summary
- Abstract
- Description
- Claims
- Application Information
AI Technical Summary
Problems solved by technology
Method used
Examples
Embodiment 1
[0017] Use enzymes, desizing agents, degreasing scouring agents and penetrating agents to cold pile gray fabrics, wash them with water washing machines, and use Fong's Monforts sizing machines for presetting treatment. After the above treatments, the fabrics are sprayed and pressure treated in machine cylinders. The water level is controlled at 3.5 tons, the bath ratio is 1:15, the speed of the fabric is adjusted by spraying pressure when the vat is running, and then 98% concentrated sulfuric acid, the dosage is 0.6g / L, added to the auxiliary vat to dilute and stir evenly. Then slowly add it into the above-mentioned machine vat, raise the temperature to 90°C, and keep it warm for 80 minutes to pickle, wash with water after pickling, neutralize with soda ash to neutrality, and then dye, and the fabric after opening can be obtained after setting.
Embodiment 2
[0019] Use enzymes, desizing agents, degreasing scouring agents and penetrating agents to cold pile gray fabrics, wash them with water washing machines, and use Fong's Monforts sizing machines for presetting treatment. After the above treatments, the fabrics are sprayed and pressure treated in machine cylinders. The water level is controlled at 4 tons, the bath ratio is 1:18, the speed of the fabric is adjusted by spraying pressure when the vat is running, and then 98% concentrated sulfuric acid is added to the auxiliary vat to dilute and stir evenly. Then slowly add it into the above-mentioned machine vat, raise the temperature to 105°C, and keep it warm for 100 minutes to pickle, wash with water after pickling, neutralize with soda ash to neutral, then dye, and set the shape to get the fabric after opening.
Embodiment 3
[0021] Use enzymes, desizing agents, degreasing scouring agents and penetrating agents to cold pile gray fabrics, wash them with water washing machines, and use Fong's Monforts sizing machines for presetting treatment. After the above treatments, the fabrics are sprayed and pressure treated in machine cylinders. Choose the water level to be controlled at 4.5 tons, and the bath ratio to be 1:20. The speed of the fabric is adjusted by spraying pressure when the vat is running, and then add 98% concentrated sulfuric acid at a dosage of 1.2g / L to the auxiliary vat to dilute and stir evenly. Then slowly add it into the above-mentioned machine vat, raise the temperature to 120°C, and keep it warm for 120 minutes for pickling, after pickling, wash with water, neutralize with soda ash to neutral, then dye, and set the shape to get the fabric after opening.
PUM
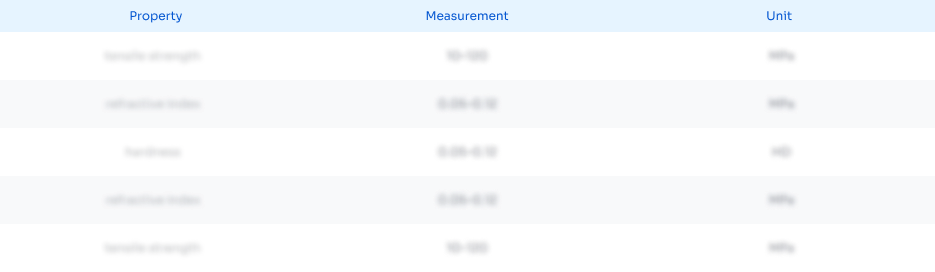
Abstract
Description
Claims
Application Information

- R&D
- Intellectual Property
- Life Sciences
- Materials
- Tech Scout
- Unparalleled Data Quality
- Higher Quality Content
- 60% Fewer Hallucinations
Browse by: Latest US Patents, China's latest patents, Technical Efficacy Thesaurus, Application Domain, Technology Topic, Popular Technical Reports.
© 2025 PatSnap. All rights reserved.Legal|Privacy policy|Modern Slavery Act Transparency Statement|Sitemap|About US| Contact US: help@patsnap.com