TFT (Thin Film Transistor) glass thinning pretreatment method
A thinning treatment and pretreatment technology, applied in the field of TFT glass thinning pretreatment, can solve the problems of surface pits, difficult control, long chemical etching time, etc.
- Summary
- Abstract
- Description
- Claims
- Application Information
AI Technical Summary
Problems solved by technology
Method used
Examples
Embodiment 1
[0018] The raw material is the TFT glass panel of the same manufacturer and batch of TFT glass AN100, the thickness of which is 1.000mm, and the size is 730mm×920mm. The etching and polishing equipment used are respectively Dongguan Hongcun etching machine and Hunan Yongchuang polishing machine.
[0019] Step 1: Inject 900L of 80% concentrated sulfuric acid into a closed storage tank container through a pump, then inject 50L of 30% concentrated hydrochloric acid, and finally add 50L of 50% hydrofluoric acid;
[0020] Step 2: Heat to 28-30°C in a closed storage tank container while bubbling and stirring evenly;
[0021] Step 3: Put the mixed acid into the acid tank of the etching machine, and keep bubbling and stirring for 30-60 minutes evenly;
[0022] Step 4: Soak 5 pieces of TFT substrates A, B, C, D, and E in the mixture for 15 minutes, and remove the double layer of 60 microns on the glass surface;
[0023] Step 5: Wash the glass surface with clean water, then enter the ...
Embodiment 2
[0029] The raw material is the same batch of TFT glass panels from the same manufacturer as Corning Glass, with a thickness of 1.000mm and a size of 730mm×920mm. The etching and polishing equipment used are respectively Dongguan Hongcun etching machine and Hunan Yongchuang polishing machine.
[0030] Step 1: Inject 900L of 80% concentrated sulfuric acid into a closed storage tank container through a pump, then inject 50L of 30% concentrated hydrochloric acid, and finally add 50L of 50% hydrofluoric acid;
[0031] Step 2: Heat to 28-30°C in a closed storage tank container while bubbling and stirring evenly;
[0032] Step 3: Put the mixed acid into the acid tank of the etching machine, and keep bubbling and stirring for 30-60 minutes evenly;
[0033] Step 4: Soak 5 pieces of TFT substrates A, B, C, D, and E in the mixture for 15 minutes, and remove the double layer of 60 microns on the glass surface;
[0034] Step 5: Wash the glass surface with clean water, then enter the hydr...
Embodiment 3
[0041] The raw material is the TFT glass panel of the same manufacturer and batch of TFT glass AN100, the thickness of which is 1.000mm, and the size is 730mm×920mm. The etching and polishing equipment used are respectively Dongguan Hongcun etching machine and Hunan Yongchuang polishing machine.
[0042] Step 1: Inject 950L of 80% concentrated sulfuric acid into a closed storage tank container through a pump, then inject 30L of 30% concentrated hydrochloric acid, and finally add 50L of 50% hydrofluoric acid;
[0043] Step 2: Heat to 28-30°C in a closed storage tank container while bubbling and stirring evenly;
[0044] Step 3: Put the mixed acid into the acid tank of the etching machine, and keep bubbling and stirring for 30-60 minutes evenly;
[0045] Step 4: Soak 5 pieces of TFT substrates A, B, C, D, and E in the mixture for 15 minutes, and remove the double layer of 60 microns on the glass surface;
[0046] Step 5: Wash the glass surface with clean water, and then enter ...
PUM
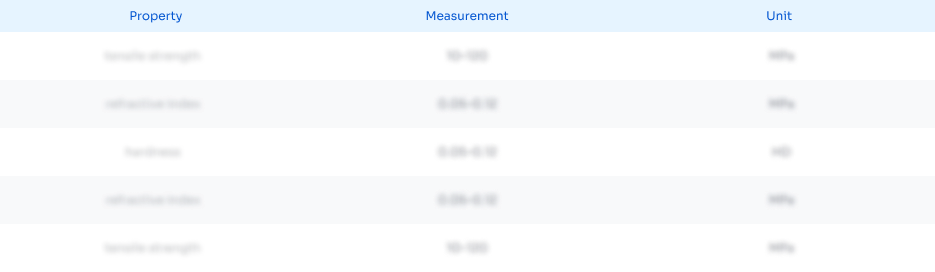
Abstract
Description
Claims
Application Information

- Generate Ideas
- Intellectual Property
- Life Sciences
- Materials
- Tech Scout
- Unparalleled Data Quality
- Higher Quality Content
- 60% Fewer Hallucinations
Browse by: Latest US Patents, China's latest patents, Technical Efficacy Thesaurus, Application Domain, Technology Topic, Popular Technical Reports.
© 2025 PatSnap. All rights reserved.Legal|Privacy policy|Modern Slavery Act Transparency Statement|Sitemap|About US| Contact US: help@patsnap.com