Novel composite riser heating agent and preparation method thereof
A heating agent, a new type of technology, applied in the direction of casting molding equipment, molds, cores, etc., can solve the problems of insufficient heat generation, poor heat preservation, difficulty in meeting the feeding requirements of castings, etc., to meet the feeding requirements and good heat preservation effect Effect
- Summary
- Abstract
- Description
- Claims
- Application Information
AI Technical Summary
Problems solved by technology
Method used
Examples
Embodiment 1
[0026] To prepare modified pulverized coal, the burnt fly ash is first placed in 20% sulfuric acid, stirred for 20 hours, filtered out, then placed in 16% sodium hydroxide solution, stirred for 20 hours, and then removed from the acid-base The fly ash filtered out of the immersion liquid is washed with deionized water until neutral, and finally obtained after filtering and drying;
[0027] Select 25 parts by weight of aluminum powder, 5 parts of magnesium powder, 3 parts of fluorite powder, 3 parts of silicon carbide powder, 5 parts of iron oxide powder, 3 parts of silicon calcium powder, 12 parts of aluminum slag, 8 parts of modified fly ash , 6 parts of sodium nitrate, and 6 parts of sodium fluorosilicate are mixed, transported to the planetary mixer mill and stirred for 100 minutes, stirred into a mixture, then sent to the conveyor and sent to the spherical mold in the packaging machine for high-pressure molding, and the formed The sphere heating agent is pushed out of the ...
Embodiment 2
[0029] To prepare modified pulverized coal, the burnt fly ash is placed in 25% sulfuric acid, stirred for 22 hours, filtered out, then placed in 24% sodium hydroxide solution, stirred for 22 hours, and then removed from the acid-base The fly ash filtered out of the immersion liquid is washed with deionized water until neutral, and finally obtained after filtering and drying;
[0030] Select 35 parts by weight of aluminum powder, 15 parts of magnesium powder, 7 parts of fluorite powder, 7 parts of silicon carbide powder, 10 parts of iron oxide powder, 7 parts of silicon calcium powder, 16 parts of aluminum slag, 12 parts of modified fly ash , 9 parts of sodium nitrate, and 9 parts of sodium fluorosilicate are mixed, transported to the planetary mixer mill and stirred for 120 minutes, stirred into a mixture, then sent to the conveyor and sent to the spherical mold in the packaging machine for high-pressure molding, and the formed The sphere heating agent is pushed out of the mol...
Embodiment 3
[0032] To prepare modified pulverized coal, put the burnt fly ash in 23% sulfuric acid, stir for 21 hours, filter out, then place in 20% sodium hydroxide solution, stir for 21 hours, and then remove from acid-base The fly ash filtered out of the immersion liquid is washed with deionized water until neutral, and finally obtained after filtering and drying;
[0033] Select 30 parts of aluminum powder, 10 parts of magnesium powder, 5 parts of fluorite powder, 5 parts of silicon carbide powder, 7 parts of iron oxide powder, 5 parts of silicon calcium powder, 14 parts of aluminum slag, and 10 parts of modified fly ash according to parts by weight , 7 parts of sodium nitrate, and 7 parts of sodium fluorosilicate are mixed, transported to the planetary mixer mill and stirred for 110 minutes, stirred into a mixture, then sent to the conveyor and sent to the spherical mold in the packaging machine for high-pressure molding, and the formed The sphere heating agent is pushed out of the m...
PUM
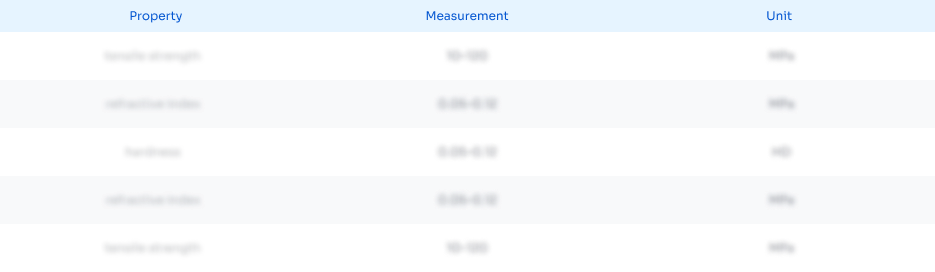
Abstract
Description
Claims
Application Information

- R&D
- Intellectual Property
- Life Sciences
- Materials
- Tech Scout
- Unparalleled Data Quality
- Higher Quality Content
- 60% Fewer Hallucinations
Browse by: Latest US Patents, China's latest patents, Technical Efficacy Thesaurus, Application Domain, Technology Topic, Popular Technical Reports.
© 2025 PatSnap. All rights reserved.Legal|Privacy policy|Modern Slavery Act Transparency Statement|Sitemap|About US| Contact US: help@patsnap.com