Low-emission low-rotational-flow combustion chamber head structure for aircraft engine
A technology for aero-engines and combustion chambers, applied in the direction of combustion chambers, continuous combustion chambers, combustion methods, etc., can solve problems such as reduction, achieve the effects of reducing pollution emissions, ensuring stability and combustion efficiency, and avoiding spontaneous combustion problems
- Summary
- Abstract
- Description
- Claims
- Application Information
AI Technical Summary
Problems solved by technology
Method used
Image
Examples
Embodiment Construction
[0027] The present invention will be further described below in conjunction with the accompanying drawings and specific embodiments.
[0028] figure 1 It is a general cross-sectional view of the head structure of the combustion chamber of the present invention. The main combustion stage is fixed on the flame cylinder through the swirler mounting plate, and then the assembled pre-combustion stage is inserted into the main combustion stage in the axial direction. The ring is matched with the inner ring of the pre-film air atomizing nozzle, so that the main combustion stage and the pre-combustion stage are assembled together in a concentric manner, the pre-combustion stage is in the center, and the main combustion stage is arranged on the periphery of the pre-combustion stage. The double oil circuit nozzles are evenly arranged along the circumference of the entire engine, and the number is 12 to 30. figure 2 It is a sectional view of the pre-combustion stage structure of the pr...
PUM
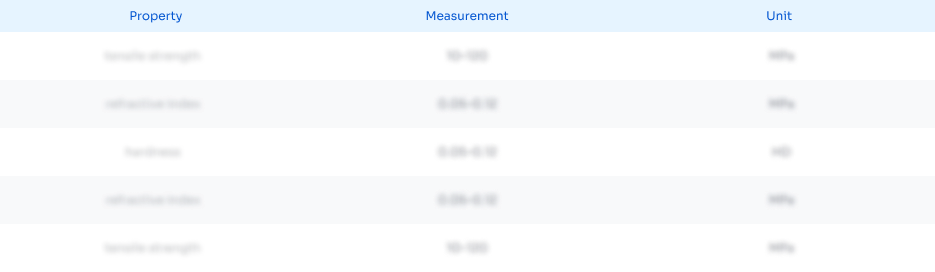
Abstract
Description
Claims
Application Information

- R&D
- Intellectual Property
- Life Sciences
- Materials
- Tech Scout
- Unparalleled Data Quality
- Higher Quality Content
- 60% Fewer Hallucinations
Browse by: Latest US Patents, China's latest patents, Technical Efficacy Thesaurus, Application Domain, Technology Topic, Popular Technical Reports.
© 2025 PatSnap. All rights reserved.Legal|Privacy policy|Modern Slavery Act Transparency Statement|Sitemap|About US| Contact US: help@patsnap.com