Method for manufacturing steel-plastic composite pipe with rotational moulded inner wall and composite glass fiber outer wall
A steel-plastic composite pipe and steel pipe inner wall technology, applied in the direction of pipes/pipe joints/fittings, pipes, rigid pipes, etc., can solve the problems of high equipment requirements and complex processes, and achieve high bonding, simple process, and strong viscosity Effect
- Summary
- Abstract
- Description
- Claims
- Application Information
AI Technical Summary
Problems solved by technology
Method used
Image
Examples
Embodiment Construction
[0029] The technical solutions of the present invention will be further specifically described below through the embodiments and in conjunction with the accompanying drawings.
[0030] In this embodiment, a steel-plastic composite pipe in which the inner wall of the steel pipe is rotomolded and the outer wall is composited with glass fiber, such as figure 1 , figure 2 As shown, the middle steel pipe layer 3 is a skeleton layer and has two structural forms. One is the whole pipe 10 structure, one end is provided with flange 1, and the other end is socket interface 5; the other is the whole pipe A101 structure, one end is welded with steel flange A8, and both flange 1 and flange A8 are provided with There is a bolt hole 9, and the other end is welded with a section of socket 7. There are two grooves on the outside of the socket 7, and the outer diameter of the socket 7 is smaller than the inner diameter of the socket interface 5. The outer diameter of the 7 parts is matched w...
PUM
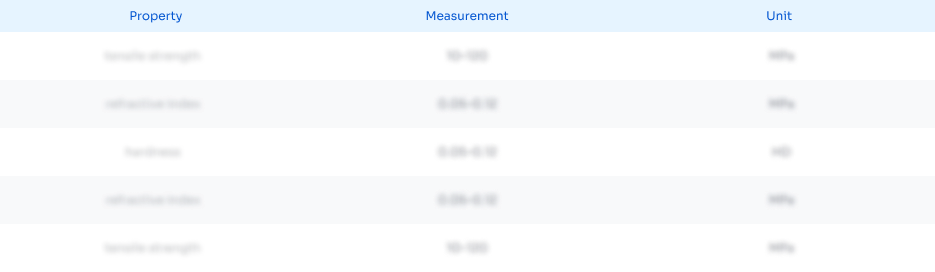
Abstract
Description
Claims
Application Information

- R&D Engineer
- R&D Manager
- IP Professional
- Industry Leading Data Capabilities
- Powerful AI technology
- Patent DNA Extraction
Browse by: Latest US Patents, China's latest patents, Technical Efficacy Thesaurus, Application Domain, Technology Topic, Popular Technical Reports.
© 2024 PatSnap. All rights reserved.Legal|Privacy policy|Modern Slavery Act Transparency Statement|Sitemap|About US| Contact US: help@patsnap.com