LF refining dephosphorization production process for low-phosphorus low-carbon steel
A production process, low-carbon steel technology, applied in the direction of improving process efficiency, etc., can solve problems such as furnace lining erosion, high end temperature of converter, large temperature drop, etc., to reduce steelmaking costs, improve product quality, and improve deep processing such as stamping performance effect
- Summary
- Abstract
- Description
- Claims
- Application Information
AI Technical Summary
Problems solved by technology
Method used
Image
Examples
Embodiment 1
[0028] A low-phosphorus and low-carbon steel LF refining and dephosphorization production process, the steel output of the converter is 130 tons, the mass percentage of the chemical composition of the product is: C: 0.017%, Si: 0.006%, Mn: 0.19%, P: 0.008%, S: 0.01%, AL: 0.03%, the rest is Fe and unavoidable impurities. Including the following process steps:
[0029] (1) Converter smelting: smelting end point mass percentage C: 0.07%, molten steel [O] 468ppm;
[0030] Final slag basicity: R3.0-3.5, slag penetration throughout the smelting process, tapping temperature 1661°C;
[0031] Converter tapping requires "bare steel" tapping without adding any deoxidized alloy materials; after tapping 1 / 4, add refining slag 300kg / furnace, lime 200kg / furnace in batches, and bottom blow argon gas during tapping;
[0032] The mass percentage of the molten steel composition in the argon blowing station out of the converter is: C: 0.058, Si: 0.005%, Mn: 0.06%, P: 0.014%, S: 0.011%, and the ...
Embodiment 2
[0042] A low-phosphorus and low-carbon steel LF refining and dephosphorization production process, the converter steel output is 130 tons, the product chemical composition mass percentage is: C: 0.016%, Si: 0.006%, Mn: 0.19%, P: 0.006%, S: 0.009%, AL: 0.04%, the rest is Fe and unavoidable impurities. Including the following process steps:
[0043] (1) Converter smelting: smelting key mass percentage: C0.069%, molten steel [O] 592ppm;
[0044] Final slag basicity: R3.0-3.5, slag penetration throughout the smelting process, tapping temperature 1652°C;
[0045] Converter tapping requires "bare steel" tapping without adding any deoxidized alloy materials; after tapping 1 / 4, add refining slag 500kg / furnace, and lime 300kg / furnace in batches, and argon gas is blown at the bottom during tapping;
[0046] The composition mass percentage of molten steel in the argon blowing station of the converter is: C: 0.055%, Si: 0.008%, Mn: 0.063%, P: 0.012%, S: 0.010%, and the rest is Fe and un...
Embodiment 3
[0056]A low-phosphorus and low-carbon steel LF refining dephosphorization production process, the converter steel output is 130 tons, the product chemical composition mass percentage is: C: 0.017%, Si: 0.005%, Mn: 0.18%, P: 0.008%, S: 0.009%, AL: 0.02%, the rest is Fe and unavoidable impurities. Including the following process steps:
[0057] (1) Converter smelting: smelting end point mass percentage C: 0.055%, molten steel [O] 604ppm;
[0058] Final slag basicity: R3.0-3.5, slag penetration throughout the smelting process, tapping temperature 1664°C;
[0059] Converter tapping requires "bare steel" tapping without adding any deoxidized alloy materials; after tapping 1 / 4, add refining slag 300kg / furnace, lime 200kg / furnace in batches, and bottom blow argon gas during tapping;
[0060] The mass percentage of molten steel out of the converter is: C: 0.049%, Si: 0.005%, Mn: 0.06%, P: 0.010%, S: 0.011%, and the rest is Fe and unavoidable impurities;
[0061] (2) LF refining: LF...
PUM
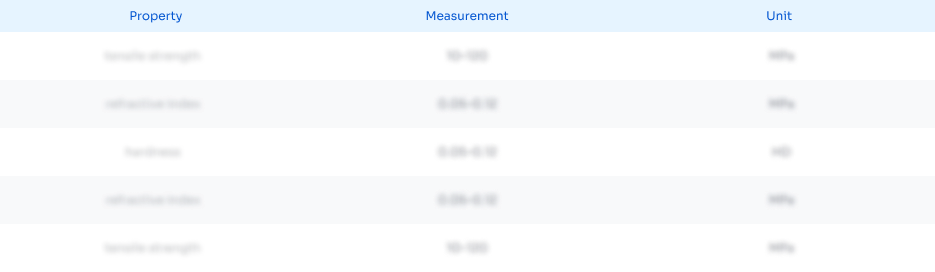
Abstract
Description
Claims
Application Information

- R&D Engineer
- R&D Manager
- IP Professional
- Industry Leading Data Capabilities
- Powerful AI technology
- Patent DNA Extraction
Browse by: Latest US Patents, China's latest patents, Technical Efficacy Thesaurus, Application Domain, Technology Topic, Popular Technical Reports.
© 2024 PatSnap. All rights reserved.Legal|Privacy policy|Modern Slavery Act Transparency Statement|Sitemap|About US| Contact US: help@patsnap.com