Method of producing rough synthesis gas by taking direct coal liquefaction residue as raw material
A technology for direct coal liquefaction and crude synthesis gas, applied in the direction of granular/powder fuel gasification, etc., can solve problems such as pollution of the environment, and achieve the effect of simple treatment process and high added value
- Summary
- Abstract
- Description
- Claims
- Application Information
AI Technical Summary
Problems solved by technology
Method used
Image
Examples
Embodiment approach
[0027] According to a typical embodiment of the present invention, the step of preparing crude synthesis gas by gasifying coal water slurry with oxygen includes: mixing coal water slurry with oxygen, and then placing the coal water slurry at 1200°C-1400°C and 4.0MPa-8.7MPa The gasification reaction is performed to obtain crude synthesis gas; and the crude synthesis gas is purified and shifted to obtain crude synthesis gas. The specific reaction temperature and pressure are determined by the melting characteristics of gasification raw ash and the pressure requirements of downstream devices.
[0028] The invention also provides a device for producing crude synthesis gas by using the coal direct liquefaction residue as a raw material. Such as figure 1 As shown, the device includes: a coal mill 10, a coal slurry storage tank 20 and a gasifier 40, the coal pulverizer 10 is provided with a feed port and a discharge port, the feed port of the coal slurry storage tank 20 is connected...
Embodiment 1
[0034] 1) Preprocessing steps
[0035] The high-temperature liquid coal direct liquefaction residue flowing out of the coal liquefaction reactor is sent to the residue forming machine to be indirectly cooled until the residue is brittle
[0036] Point below, and then molded into 2 ~ 8mm flake solid.
[0037] 2) Preparation of coal water slurry step
[0038]The flaky coal pretreated in step 1) is directly liquefied residue, ground in a coal mill until 99% of the particle size is less than 1mm, and added water during the grinding process, and added modified lignin additive, to obtain a residue slurry with a mass percentage concentration of 70%; put the raw coal in another coal mill to grind to 99% of the particle size is less than 1mm, and add water to pulp during the grinding process. The modified lignin additive is added to obtain a raw coal slurry with a mass percentage concentration of 60%.
[0039] Send the residue slurry and raw coal slurry (mixed according to the dry b...
Embodiment 2
[0041] The operation steps and raw materials are the same as those in Example 1, except that the residue slurry and raw coal slurry (mixed at a ratio of 70:30 on a dry basis) are sent into a coal slurry storage tank for stirring and mixing to obtain a coal-water slurry with a concentration of 64wt%. .
PUM
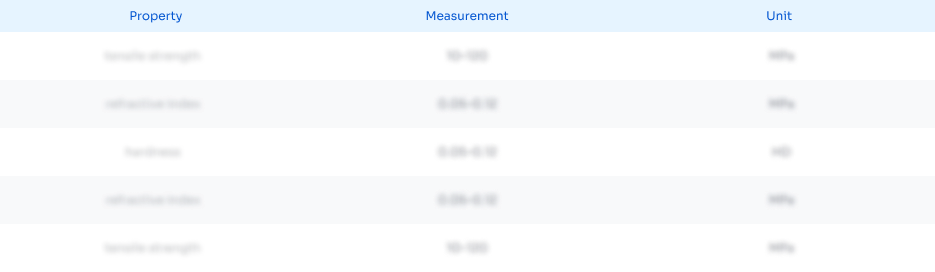
Abstract
Description
Claims
Application Information

- R&D
- Intellectual Property
- Life Sciences
- Materials
- Tech Scout
- Unparalleled Data Quality
- Higher Quality Content
- 60% Fewer Hallucinations
Browse by: Latest US Patents, China's latest patents, Technical Efficacy Thesaurus, Application Domain, Technology Topic, Popular Technical Reports.
© 2025 PatSnap. All rights reserved.Legal|Privacy policy|Modern Slavery Act Transparency Statement|Sitemap|About US| Contact US: help@patsnap.com