Differential pressure forming method for local large-deformation hollow pieces
A technology of large deformation and hollow parts, which is applied in the differential pressure forming of hollow parts and the differential pressure forming of hollow parts with local large deformation, which can solve the problems that the balance punch is difficult to function, the local expansion rate and the complex mold structure cannot be solved. , to achieve the effect of convenient feeding and final forming, simple structure and increasing bulging limit
- Summary
- Abstract
- Description
- Claims
- Application Information
AI Technical Summary
Problems solved by technology
Method used
Image
Examples
Embodiment 1
[0025] In the first step, the surface of the 304 stainless steel tube blank 2 with a diameter of 50mm, a length of 300mm and a wall thickness of 2mm is cleaned and put into the convex mold 1, and the upper and lower molds are closed;
[0026] In the second step, the punch 3 is loaded into the tube blank and sealed;
[0027] The third step is to inject hydraulic oil 4 into the inside of the tube blank 2 and the outer surface of the tube blank (that is, the inside of the mold 1) at the same time, and quickly increase the hydraulic pressure inside the tube blank 2 to 45MPa, and the hydraulic pressure outside the tube blank 2 to 7MPa , and then slowly increase the hydraulic pressure inside and outside the tube blank 2 at the same time, control the hydraulic pressure inside the tube blank 2 to basically maintain at 50MPa during the working stage, and maintain the hydraulic pressure outside the tube blank 2 at 10MPa during the working stage, control the inside of the tube blank, the ...
Embodiment 2
[0031] The first step is to clean the surface of 20 steel tube blanks with a diameter of 40 mm, a length of 500 mm, and a wall thickness of 2 mm, and then put them into a stepped mold, and the upper and lower molds are closed;
[0032] The second step is to put the punch into the tube blank and seal it;
[0033] The third step is to inject high-pressure liquid into the inside of the tube blank and the outer surface of the tube blank (that is, the inside of the mold) at the same time, quickly increase the hydraulic pressure inside the tube blank to 40MPa, and increase the hydraulic pressure outside the tube blank to 7MPa, and then increase slowly The hydraulic pressure inside and outside the tube blank is controlled to maintain the hydraulic pressure inside the tube blank at 45MPa during the working stage, the hydraulic pressure outside the tube blank is basically maintained at 10MPa during the working stage, and the pressure difference between the inside and outside of the tube...
Embodiment 3
[0037] The first step is to clean the surface of the 304 stainless steel tube blank with a diameter of 30mm, a length of 400mm and a wall thickness of 2mm and put it into the three-way mold, and the upper and lower molds are closed;
[0038] The second step is to put the punch into the tube blank and seal it;
[0039] The third step is to inject water into the tube blank, inject hydraulic oil into the outer surface of the tube blank (that is, inside the mold), quickly increase the hydraulic pressure inside the tube blank to 60 MPa, and increase the hydraulic pressure outside the tube blank to 3 MPa, and then Slowly increase the hydraulic pressure inside and outside the tube blank, control the hydraulic pressure inside the tube blank to basically maintain at 65MPa during the working stage, maintain the hydraulic pressure outside the tube blank at 5MPa during the working stage, and control the pressure difference between the inside and outside of the tube blank to 60MPa;
[0040...
PUM
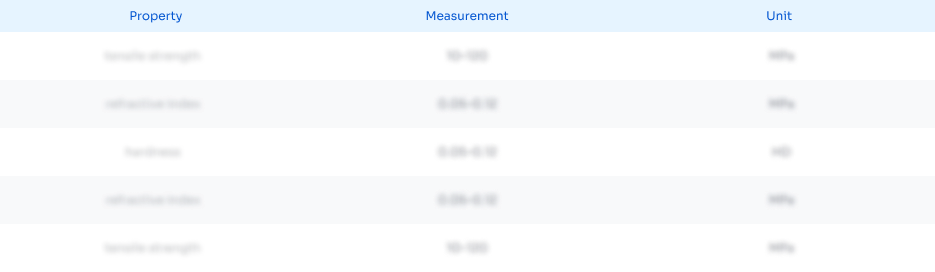
Abstract
Description
Claims
Application Information

- R&D
- Intellectual Property
- Life Sciences
- Materials
- Tech Scout
- Unparalleled Data Quality
- Higher Quality Content
- 60% Fewer Hallucinations
Browse by: Latest US Patents, China's latest patents, Technical Efficacy Thesaurus, Application Domain, Technology Topic, Popular Technical Reports.
© 2025 PatSnap. All rights reserved.Legal|Privacy policy|Modern Slavery Act Transparency Statement|Sitemap|About US| Contact US: help@patsnap.com