Sintered filter core cleaning device and method
A technology of sintered filter elements and cleaning devices, applied in separation methods, chemical instruments and methods, filtration and separation, etc., can solve the problems of reducing equipment service life, affecting filtration efficiency, and high degree of impurity adhesion, so as to extend the cycle of off-line cleaning , optimize the treatment process, improve the effect of service life
- Summary
- Abstract
- Description
- Claims
- Application Information
AI Technical Summary
Problems solved by technology
Method used
Image
Examples
Embodiment Construction
[0017] Such as figure 1 Shown, the specific embodiment of the present invention mainly comprises the following steps: soaking with solvent dimethylacetamide is full of solvent tank, the metal powder sintered filter core of viscose spinning is taken out from filter and puts into solvent tank to soak 12-24 hours, the temperature is controlled at 90°C, so that the viscose on the surface of the filter element and in the pores is fully dissolved, soaked and dried naturally. Put the filter element into the heating furnace, slowly heat up at 100-350°C, control the baking time at 2-4 hours, remove organic dirt, carbonize the polymer in the micropores, and take it out after cooling down. Put the filter element into the lye tank of 5-15% sodium hydroxide solution, boil it, and soak in lye for 2-4 hours. Take out the filter element from the lye tank, use a high-pressure water gun to repeatedly rinse the filter element from the outside to the inside, and from the inside to the outside of...
PUM
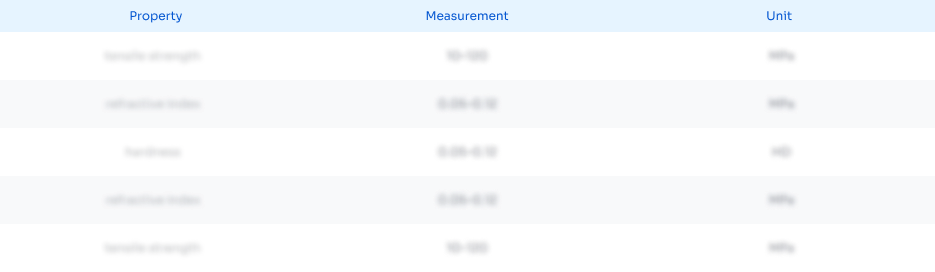
Abstract
Description
Claims
Application Information

- R&D Engineer
- R&D Manager
- IP Professional
- Industry Leading Data Capabilities
- Powerful AI technology
- Patent DNA Extraction
Browse by: Latest US Patents, China's latest patents, Technical Efficacy Thesaurus, Application Domain, Technology Topic, Popular Technical Reports.
© 2024 PatSnap. All rights reserved.Legal|Privacy policy|Modern Slavery Act Transparency Statement|Sitemap|About US| Contact US: help@patsnap.com