Modified polyformaldehyde supporting material for 3D printing and preparation method thereof
A technology of 3D printing and supporting materials, applied in the field of new materials, can solve the problem of undisclosed polyoxymethylene
- Summary
- Abstract
- Description
- Claims
- Application Information
AI Technical Summary
Problems solved by technology
Method used
Examples
Embodiment 1
[0021] 8 kg of pre-dried polyformaldehyde, 0.7 kg of silicone oil, and 1.3 kg of calcium carbonate are mixed in a plastic mixer for 1 minute and discharged. The mixed materials are blended and pelletized in a single / twin screw extruder, and the temperature of the extruder is set at 180°C to prepare a support material for 3D printing. When printing, put the prepared 1.75mm or 3mm polyoxymethylene wire in the 3D printer's material box, the print head can be set at 200-220℃, the hot bed temperature can be at 50-90℃, and the printing speed can be set at 25- 75mm / s, after the print head and hot bed rise to the set temperature, start printing and molding. After printing, place the printed product in a dilute hydrochloric acid solution. After about 30 minutes, the POM printed and molded part will melt.
Embodiment 2
[0023] Mix 8.5 kg of pre-dried polyformaldehyde, 0.4 kg of paraffin wax, and 1.1 kg of talc in a plastic mixer for 1 minute and discharge. The mixed material is blended and pelletized in a single / twin screw extruder, and the temperature of the extruder is set at 170°C to prepare a support material for 3D printing, which can be dissolved in an acid solution. When printing, put the prepared 1.75mm or 3mm polyoxymethylene wire in the 3D printer's material box, the print head can be set at 200-220℃, the hot bed temperature can be at 50-90℃, and the printing speed can be set at 25- 75mm / s, after the print head and hot bed rise to the set temperature, start printing and molding. After printing, place the printed product in a dilute hydrochloric acid solution. After about 30 minutes, the POM printed and molded part will melt.
Embodiment 3
[0025] Mix 9 kg of pre-dried polyformaldehyde, 0.2 kg of titanate, 0.8 kg of calcium carbonate and talc in a plastic mixer for 2 minutes, and then discharge. The mixed materials are blended and pelletized in a twin-screw extruder. The temperature of the extruder is set at 185°C to prepare a support material for 3D printing, which can be decomposed in acid gas. When printing, put the prepared 1.75mm or 3mm polyoxymethylene wire in the 3D printer's material box, the print head can be set at 200-220℃, the hot bed temperature can be at 50-90℃, and the printing speed can be set at 25- 75mm / s, after the print head and hot bed rise to the set temperature, start printing and molding. After printing, place the printed product in a dilute hydrochloric acid solution. After about 30 minutes, the POM printed and molded part will melt.
PUM
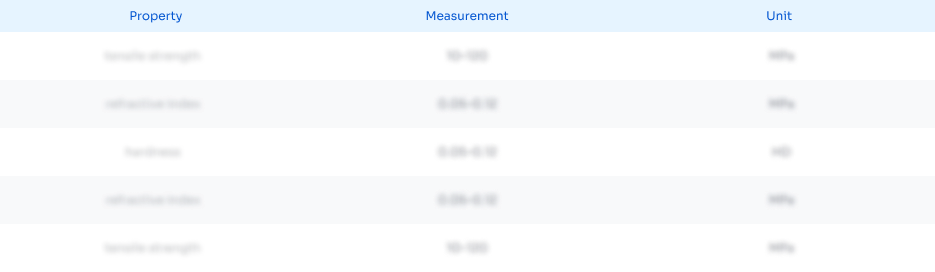
Abstract
Description
Claims
Application Information

- R&D
- Intellectual Property
- Life Sciences
- Materials
- Tech Scout
- Unparalleled Data Quality
- Higher Quality Content
- 60% Fewer Hallucinations
Browse by: Latest US Patents, China's latest patents, Technical Efficacy Thesaurus, Application Domain, Technology Topic, Popular Technical Reports.
© 2025 PatSnap. All rights reserved.Legal|Privacy policy|Modern Slavery Act Transparency Statement|Sitemap|About US| Contact US: help@patsnap.com