Wave-absorbing material and preparation method thereof
A technology of wave absorbing material and wave absorbing agent, applied in the field of wave absorbing material, can solve the problems of difficult to increase filling concentration, high cost, complicated process method, etc., and achieve good electromagnetic wave absorption performance, maintain integrity, and high magnetic permeability. Effect
- Summary
- Abstract
- Description
- Claims
- Application Information
AI Technical Summary
Problems solved by technology
Method used
Image
Examples
Embodiment 1
[0031] A kind of absorbing material, raw material comprises by mass part:
[0032]
[0033] The thermosetting elastomer is EPDM rubber.
[0034] The absorbing agent is sendust.
[0035] Described curing agent is dicumyl peroxide.
[0036] Described accelerator is accelerator D.
[0037] Described solvent is toluene.
[0038] The sheet diameter of the sheet-shaped wave absorbing agent is 20 μm, and the ratio of sheet diameter to thickness is 50:1.
[0039] This embodiment provides a method for preparing a wave-absorbing material, comprising the following steps:
[0040] (1) Dissolution of the matrix: Weigh the mass parts of the thermosetting elastomer, curing agent, and accelerator and dissolve them into the mass parts of the solvent, heat and stir at a high speed to form a solution, the heating temperature is 50 ° C, and the stirring rate is 1000 rpm ;Continue to stir for 10min after all dissolved;
[0041] (2) Mixing of the matrix and the wave absorbing agent: Weigh ...
Embodiment 2
[0045] A kind of absorbing material, raw material comprises by mass part:
[0046]
[0047] The thermosetting elastomer is nitrile rubber.
[0048] The absorbing agent is FeSiCr.
[0049] Described curing agent is benzoyl peroxide.
[0050] The accelerator is accelerator TMTD.
[0051] Described solvent is chlorinated hydrocarbon.
[0052] The sheet diameter of the sheet-shaped wave absorbing agent is 70 μm, and the ratio of sheet diameter to thickness is 150:1.
[0053] This embodiment provides a method for preparing a wave-absorbing material, comprising the following steps:
[0054] (1) Dissolution of the matrix: Weigh the mass parts of the thermosetting elastomer, curing agent, and accelerator and dissolve them into the mass parts of the solvent, heat and stir at a high speed to form a solution, the heating temperature is 80 °C, and the stirring rate is 3000 rpm ; Continue to stir for 60min after all dissolve;
[0055] (2) Mixing of the matrix and the wave absorbing ...
Embodiment 3
[0059] A kind of absorbing material, raw material comprises by mass part:
[0060]
[0061] The thermosetting elastomer is neoprene.
[0062] The wave absorbing agent is iron silicon nickel.
[0063] Described curing agent is tert-butyl benzoyl peroxide.
[0064] Accelerator TMTM.
[0065] Described solvent is butanone.
[0066] The sheet diameter of the sheet-shaped wave absorbing agent is 50 μm, and the ratio of sheet diameter to thickness is 100:1.
[0067] This embodiment provides a method for preparing a wave-absorbing material, comprising the following steps:
[0068] (1) Dissolution of the matrix: Weigh the mass parts of the thermosetting elastomer, curing agent, and accelerator and dissolve them into the mass parts of the solvent, heat and stir at a high speed to form a solution, the heating temperature is 65 ° C, and the stirring rate is 2000 rpm ; Continue to stir for 45min after all dissolved;
[0069] (2) Mixing of the matrix and the wave absorbing agent: ...
PUM
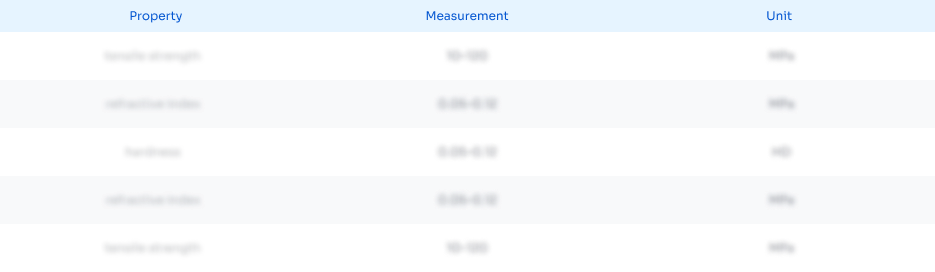
Abstract
Description
Claims
Application Information

- Generate Ideas
- Intellectual Property
- Life Sciences
- Materials
- Tech Scout
- Unparalleled Data Quality
- Higher Quality Content
- 60% Fewer Hallucinations
Browse by: Latest US Patents, China's latest patents, Technical Efficacy Thesaurus, Application Domain, Technology Topic, Popular Technical Reports.
© 2025 PatSnap. All rights reserved.Legal|Privacy policy|Modern Slavery Act Transparency Statement|Sitemap|About US| Contact US: help@patsnap.com