Manufacturing method for novel shadow mask for producing OLED display panel
A manufacturing method and display panel technology, applied in the direction of ion implantation plating, metal material coating process, coating, etc., can solve the problems of difficult control of etching precision, high etching rejection rate, and difficult chemical etching, etc. , to achieve the effects of shortening the etching cycle, simplifying the manufacturing process, and facilitating etching
- Summary
- Abstract
- Description
- Claims
- Application Information
AI Technical Summary
Problems solved by technology
Method used
Image
Examples
Embodiment Construction
[0047] A method for making a novel shadow mask for OLED display panel production, the structure of the shadow mask 1 is as follows: figure 1 , figure 2 , image 3 As shown, in this embodiment, only the creation of a fine graphics area is taken as an example for illustration.
[0048] 1. Preparation of substrate or frame
[0049] Made of stainless steel or Invar (Invar) such as Figure 4 , Figure 5 Substrate or frame workpiece with single or multiple through holes2 as shown. According to the size and complexity of the fine mask plate, there may be one or more through holes. The size of the through hole is 0.5-3mm longer than each side of the mask pattern actually required, and the center of the through hole coincides with the center of the mask pattern. The reason why the size of the through hole is 0.5-3mm longer than the sides of the actual required mask pattern is: one is that the present invention adopts the method of inlaying fillers, in order to ensure the one-to-...
PUM
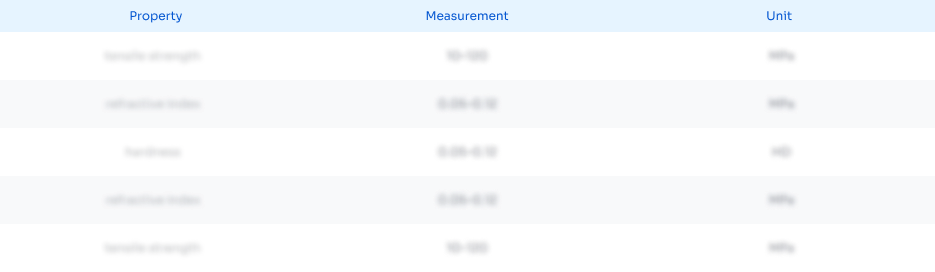
Abstract
Description
Claims
Application Information

- R&D
- Intellectual Property
- Life Sciences
- Materials
- Tech Scout
- Unparalleled Data Quality
- Higher Quality Content
- 60% Fewer Hallucinations
Browse by: Latest US Patents, China's latest patents, Technical Efficacy Thesaurus, Application Domain, Technology Topic, Popular Technical Reports.
© 2025 PatSnap. All rights reserved.Legal|Privacy policy|Modern Slavery Act Transparency Statement|Sitemap|About US| Contact US: help@patsnap.com