Method for synthesizing 2-ethyl-2-hexenal
A technology of hexenal and ethyl hexanol, which is applied in the field of synthesizing 2-ethyl-2-hexenal, can solve the problems of increasing energy consumption and material consumption, reducing the concentration of butyraldehyde in the liquid phase, disadvantages, etc.
- Summary
- Abstract
- Description
- Claims
- Application Information
AI Technical Summary
Problems solved by technology
Method used
Image
Examples
Embodiment 1
[0020] 10g of MgO / Al with a Mg / Al ratio of 1.25 was loaded into the fixed bed reactor 2 o 3 The solid base catalyst is replaced by nitrogen gas, the reaction temperature is set at 80°C, and the solvent 2-ethylhexanol is added to completely wet the catalyst. Under the conditions of butyraldehyde feed rate of 10 g / h, mass ratio of 2-ethylhexanol to butyraldehyde of 0.1, and reaction pressure of 0.1 MPa, butyraldehyde was condensed and dehydrated to generate 2-ethyl-2-hexenal. The reaction product was distilled at 0.1MPa and 100°C. The butyraldehyde extracted from the top of the tower is returned to the raw material inlet, and after the extraction from the tower kettle is chromatographically separated to separate the water phase, the organic phase is analyzed by gas chromatography. The reaction was carried out for 48 hours, the single-pass conversion rate of butyraldehyde was 63.51%, and the overall yield of 2-ethyl-2-hexenal was 95.71%. After the reaction, the catalyst Mg / Al ...
Embodiment 2
[0022] 10g of MgO / Al with a Mg / Al ratio of 1.25 was loaded into the fixed bed reactor 2 o 3 The solid base catalyst is replaced by nitrogen gas, the reaction temperature is set at 120° C., and the solvent 2-ethylhexanol is added to completely wet the catalyst. Under the conditions of butyraldehyde feed rate of 10 g / h, mass ratio of 2-ethylhexanol to butyraldehyde of 1, and reaction pressure of 0.2 MPa, butyraldehyde was condensed and dehydrated to generate 2-ethyl-2-hexenal. The reaction product was distilled at 0.15MPa and 110°C. The butyraldehyde extracted from the top of the tower is returned to the raw material inlet, and after the extraction from the tower kettle is chromatographically separated to separate the water phase, the organic phase is analyzed by gas chromatography. The reaction was carried out for 48 hours, the single-pass conversion rate of butyraldehyde was 80.03%, and the overall yield of 2-ethyl-2-hexenal was 96.26%. After the reaction, the catalyst Mg / A...
Embodiment 3
[0024] 10g of MgO / Al with a Mg / Al ratio of 1.25 was loaded into the fixed bed reactor 2 o 3 The solid base catalyst is replaced by nitrogen gas, the reaction temperature is set at 120° C., and the solvent 2-ethylhexanol is added to completely wet the catalyst. Under the conditions of butyraldehyde feed rate of 10g / h, mass ratio of 2-ethylhexanol to butyraldehyde of 3, and reaction pressure of 0.2MPa, butyraldehyde was condensed and dehydrated to generate 2-ethyl-2-hexenal. The reaction product was distilled at 0.12MPa and 110°C. The butyraldehyde extracted from the top of the tower is returned to the raw material inlet, and after the extraction from the tower kettle is chromatographically separated to separate the water phase, the organic phase is analyzed by gas chromatography. The reaction was carried out for 48 hours, the single-pass conversion rate of butyraldehyde was 75.74%, and the overall yield of 2-ethyl-2-hexenal was 96.45%. After the reaction, the catalyst Mg / Al ...
PUM
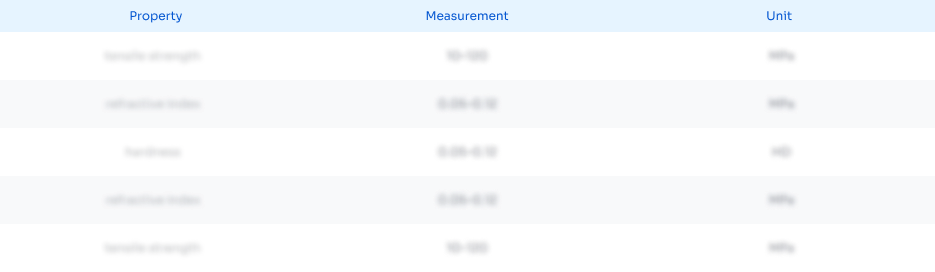
Abstract
Description
Claims
Application Information

- R&D
- Intellectual Property
- Life Sciences
- Materials
- Tech Scout
- Unparalleled Data Quality
- Higher Quality Content
- 60% Fewer Hallucinations
Browse by: Latest US Patents, China's latest patents, Technical Efficacy Thesaurus, Application Domain, Technology Topic, Popular Technical Reports.
© 2025 PatSnap. All rights reserved.Legal|Privacy policy|Modern Slavery Act Transparency Statement|Sitemap|About US| Contact US: help@patsnap.com