Technique for processing methanol-to-propylene by-products
A technology for preparing propylene from methanol and processing technology, which is applied in the field of aromatics chemical industry, can solve the problems of unreported processing technology of MTP by-products, etc., and achieves the effects of high aromatics yield and low energy consumption.
- Summary
- Abstract
- Description
- Claims
- Application Information
AI Technical Summary
Problems solved by technology
Method used
Image
Examples
Embodiment 1
[0032] (1) Aromatization of MTP liquid hydrocarbon by-products
[0033] The liquid hydrocarbon by-products of the MTP process first enter the first-stage olefin aromatization reactor. The catalyst is nano ZSM-5 molecular sieve modified by hydrothermal treatment at 450°C. The reaction temperature is 280°C, the pressure is 0.5MPa, and the mass space velocity is 1.0 h -1 react under the conditions. Then enter the second-stage alkane aromatization reactor, the catalyst is a ZSM-5 molecular sieve catalyst modified by Zn and Ni, wherein the loading of ZnO is 2.0wt%, and the loading of NiO is 1.0wt%. The reaction conditions are temperature 380°C, pressure 0.5MPa, mass space velocity 1.0h -1 . The properties of the MTP liquid hydrocarbon by-product raw materials are shown in Table 1, and the reaction results are shown in Table 2.
[0034] (2) Aromatization of by-products of MTP liquefied petroleum gas
[0035] The by-products of MTP liquefied gas and methanol are used as raw mate...
Embodiment 2
[0037] (1) Aromatization of MTP liquid hydrocarbon by-products
[0038] The liquid hydrocarbon by-products of the MTP process first enter the first-stage olefin aromatization reactor. The catalyst is nano ZSM-5 molecular sieve modified by hydrothermal treatment at 550°C. The reaction temperature is 300°C, the pressure is 1.0MPa, and the mass space velocity is 2.0 h -1 react under the conditions. Then enter the two-stage alkane aromatization reactor, the catalyst is ZSM-5 molecular sieve catalyst modified by Zn, Ni, La, the loading of ZnO is 2.0wt%, the loading of NiO is 1.0wt%, La 2 o 3 The loading amount is 1.0wt%. The reaction conditions are temperature 420°C, pressure 1.0MPa, mass space velocity 1.0h -1 , and the reaction results are shown in Table 2.
[0039] (2) Aromatization of by-products of MTP liquefied petroleum gas
[0040] The by-products of MTP liquefied gas and methanol are used as raw materials, and the properties of the liquefied gas raw materials are sho...
Embodiment 3
[0042] (1) Aromatization of MTP liquid hydrocarbon by-products
[0043] The liquid hydrocarbon by-products of the MTP process first enter the first-stage olefin aromatization reactor. The catalyst is nano ZSM-5 molecular sieve modified by hydrothermal treatment at 600°C. The reaction temperature is 340°C, the pressure is 0.5MPa, and the mass space velocity is 4.0 h -1 react under the conditions. Then enter the second-stage alkane aromatization reactor, the catalyst is ZSM-5 molecular sieve catalyst modified by Zn and Cr, the loading of ZnO is 2.0wt%, Cr 2 o 3 The loading amount is 3.0wt%. The reaction conditions are temperature 450°C, pressure 0.5MPa, mass space velocity 3.0h -1 , and the reaction results are shown in Table 2.
[0044] (2) Aromatization of MTP liquefied gas by-products
[0045] The by-products of MTP liquefied gas and methanol are used as raw materials, and the properties of the liquefied gas raw materials are shown in Table 3. Liquefied petroleum gas m...
PUM
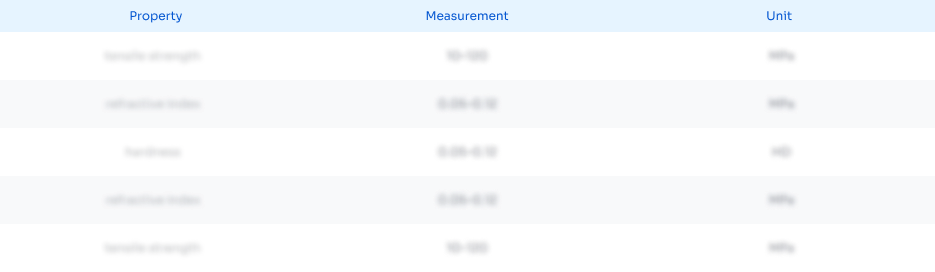
Abstract
Description
Claims
Application Information

- R&D
- Intellectual Property
- Life Sciences
- Materials
- Tech Scout
- Unparalleled Data Quality
- Higher Quality Content
- 60% Fewer Hallucinations
Browse by: Latest US Patents, China's latest patents, Technical Efficacy Thesaurus, Application Domain, Technology Topic, Popular Technical Reports.
© 2025 PatSnap. All rights reserved.Legal|Privacy policy|Modern Slavery Act Transparency Statement|Sitemap|About US| Contact US: help@patsnap.com