In-situ preparation method of magnesium borate-magnesium oxide multiphase superconducting material with different superconducting phase contents
A superconducting material, in-situ preparation technology, applied in the manufacture/processing of superconductor devices, etc., can solve the unsolved problems of in-situ regulation of superconducting phase content, inability to obtain superconducting composite materials, etc.
- Summary
- Abstract
- Description
- Claims
- Application Information
AI Technical Summary
Problems solved by technology
Method used
Image
Examples
Embodiment 1
[0014] 1. Preparation of substrate. Take a certain amount of B, Mg and B in a molar ratio of 2: 5: 1 2 o 3 After the powder is dried, it is weighed according to the predetermined molar ratio, fully ground, and pressed into a block by a tablet machine;
[0015] 2. The sealing of the base material. The specific steps are as follows: press the above-mentioned ground raw materials into blocks, put them into a ceramic crucible, cover them with a ceramic inner cover, and then sprinkle an appropriate amount of B 2 o 3 powder;
[0016] 3. Sintering of the base material. The above samples were sintered in a vacuum sintering furnace. During sintering, the following steps are followed: first, heat up to 420°C for half an hour (to form a protective barrier between the raw material and the outside world), then heat up to 620°C for 1 hour, and then heat up to 820°C for 2 hours. Finally, naturally cool to room temperature under vacuum atmosphere;
[0017] Through standard four-lead r...
Embodiment 2
[0019] 1. Preparation of substrate. Take a certain amount of powder B, Mg and B at a molar ratio of 6:7:1 2 o 3 After drying, it is weighed according to the predetermined molar ratio, fully ground, and pressed into a block by a tablet press;
[0020] 2. The sealing of the base material. The specific steps are as follows: press the above-mentioned ground raw materials into blocks, put them into a ceramic crucible, cover them with a ceramic inner cover, and then sprinkle an appropriate amount of B 2 o 3 powder;
[0021] 3. Sintering of the base material. The above samples were sintered in a vacuum sintering furnace. During sintering, the following steps are followed: first, heat up to 450°C for half an hour (to form a protective barrier between the raw material and the outside world), then heat up to 650°C for 1 hour, and then heat up to 850°C for 2 hours. Finally, naturally cool to room temperature under vacuum atmosphere;
[0022] Through standard four-lead resistance ...
Embodiment 3
[0024] 1. Preparation of substrate. Take a certain amount of B, Mg and B at a molar ratio of 10:9:1 2 o 3 After the powder is dried, it is weighed according to the predetermined molar ratio, fully ground, and pressed into a block by a tablet machine;
[0025] 2. The sealing of the base material. The specific steps are as follows: press the above-mentioned ground raw materials into blocks, put them into a ceramic crucible, cover them with a ceramic inner cover, and then sprinkle an appropriate amount of B 2 o 3 powder;
[0026] 3. Sintering of the base material. The above samples were sintered in a vacuum sintering furnace. During sintering, the following steps are followed: first, heat up to 420°C for half an hour (to form a protective barrier between the raw material and the outside world), then heat up to 620°C for 1 hour, and then heat up to 820°C for 2 hours. Finally, naturally cool to room temperature under vacuum atmosphere;
[0027] Through standard four-lead re...
PUM
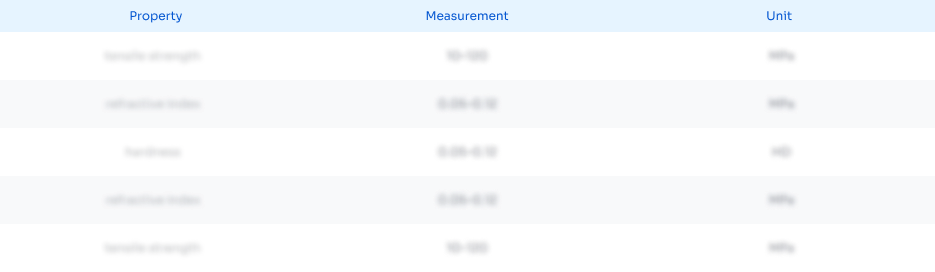
Abstract
Description
Claims
Application Information

- R&D
- Intellectual Property
- Life Sciences
- Materials
- Tech Scout
- Unparalleled Data Quality
- Higher Quality Content
- 60% Fewer Hallucinations
Browse by: Latest US Patents, China's latest patents, Technical Efficacy Thesaurus, Application Domain, Technology Topic, Popular Technical Reports.
© 2025 PatSnap. All rights reserved.Legal|Privacy policy|Modern Slavery Act Transparency Statement|Sitemap|About US| Contact US: help@patsnap.com