Preparation method of metal hafnium raw material for iodization
A technology of iodination and raw materials, which is applied in the field of raw material preparation, can solve the problems of affecting the deposition rate of iodination reaction, unfavorable iodination furnace loading and discharge, and reducing production efficiency, so as to facilitate iodination operation, improve iodination efficiency, and prevent poisoning effect
- Summary
- Abstract
- Description
- Claims
- Application Information
AI Technical Summary
Problems solved by technology
Method used
Examples
preparation example Construction
[0027] The present invention is used for the preparation method of the raw material of metal hafnium iodide, comprises the steps:
[0028] a. Press the hafnium powder under a certain pressure into a hafnium block of a certain shape; the purity of the hafnium powder is greater than 90wt%, and the particle size is less than 1mm; the pressure during pressing is 1~5Mpa; the shape of the compact is cuboid or cylinder, cuboid The size is (length>5mm)×(width>5)×(height>5mm), and the typical size is (10~200mm)×(10~80mm)×(10~80mm).
[0029] b. Dry the compact at a certain temperature for several hours; the drying temperature is 40-200° C., and the drying time is 1-50 hours. The compact must be completely dehydrated.
[0030] c. Then put the compact into a crucible and put it into a vacuum tungsten wire furnace for vacuum sintering; the temperature of vacuum sintering is not lower than 500°C, and the optimum temperature is 500~1800°C; the vacuum degree of vacuum sintering must be not lo...
Embodiment 1
[0034] The hafnium powder with a purity of 90wt% and a particle size of less than 1mm was pressed into a compact of 10mm×10m×10mm under a pressure of 1Mpa. The compact was baked at a temperature of 40° C. for 1 hour to remove moisture in the compact. Put the dried compact into a molybdenum crucible and place it in a vacuum tungsten wire furnace for vacuum sintering with a vacuum degree of 5.0×10 -1 Pa; Heating is carried out by means of segmented heat preservation, at 200°C for 0.5h, and the final sintering temperature is 500°C, with heat preservation for 1h. The purity of the finally obtained hafnium block is above 95wt%, the hydrogen content is less than 1000ppm, and the pores are evenly distributed.
Embodiment 2
[0036] The hafnium powder with a purity of 90% and a particle size of less than 1mm was pressed into a compact of 50mm×30mm×30mm under a pressure of 2Mpa. The compact was baked at a temperature of 100° C. for 5 hours to remove moisture in the compact. Put the dried compact into a tantalum crucible and place it in a vacuum tungsten wire furnace for vacuum sintering with a vacuum degree of 4.0×10 -2 Pa; Heating is carried out by means of segmented heat preservation, at 200°C for 1h, and the final sintering temperature is 900°C, and hold for 3h. The resulting hafnium block has a purity of 96.5%, a hydrogen content of less than 1000ppm, and a uniform pore size distribution.
PUM
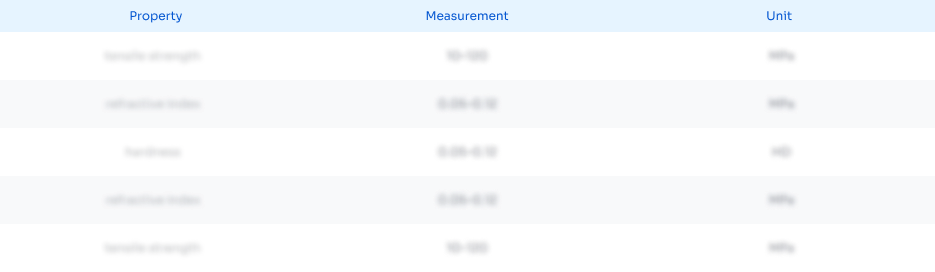
Abstract
Description
Claims
Application Information

- R&D Engineer
- R&D Manager
- IP Professional
- Industry Leading Data Capabilities
- Powerful AI technology
- Patent DNA Extraction
Browse by: Latest US Patents, China's latest patents, Technical Efficacy Thesaurus, Application Domain, Technology Topic, Popular Technical Reports.
© 2024 PatSnap. All rights reserved.Legal|Privacy policy|Modern Slavery Act Transparency Statement|Sitemap|About US| Contact US: help@patsnap.com