Method for manufacturing conductive graphene film through ink-jet printing
A conductive film and inkjet printing technology, which is applied to the conductive layer, circuit, and electrical components on the insulating carrier, can solve problems such as unsatisfactory performance, decreased electrical conductivity, and inability to fully restore the electronic structure of graphene. The effect of uniform distribution, low cost and short cycle
- Summary
- Abstract
- Description
- Claims
- Application Information
AI Technical Summary
Problems solved by technology
Method used
Examples
Embodiment 1
[0024] Measure and mix 50ml of ethanol and 50ml of dimethylformamide, add 1g of ethyl cellulose, and add 3g of graphite into ethyl cellulose (EC) / ethanol / dimethylformamide organic solvent; ultrasonic treatment for 60 minutes, power 100W, temperature 4-6°C; high-speed centrifugation at 10,000 rpm for 40 minutes, take the upper layer liquid, add 25ml NaCl aqueous solution (0.05g / ml) for flocculation, and obtain graphene powder after filtration; disperse the graphene powder in an organic solvent (cyclohexane The ratio of ketone to terpineol is 60:40), and it is made into inkjet ink, and the viscosity is adjusted to 10mPa·s, and the surface tension is 30mNm -1 ; Inject the ink into the ink cartridge, and deposit it on the pre-treated PI substrate according to the predetermined pattern using conventional inkjet printing technology; dry the conductive film deposited on the substrate in an oven, and heat-treat it at 300°C for 20 minutes to form graphite vinyl conductive film.
[002...
Embodiment 2
[0027] Measure and mix 30ml of ethanol with 70ml of dimethylformamide, add 2g of ethyl cellulose, and add 5g of graphite into ethyl cellulose (EC) / ethanol / dimethylformamide organic solvent; ultrasonic treatment for 80 minutes, power 200W, temperature 4-6°C; high-speed centrifugation at 10,000 rpm for 90 minutes, take the upper layer liquid, add 50ml NaCl aqueous solution (0.05g / ml) for flocculation, and obtain graphene powder after filtration; disperse the graphene powder in an organic solvent (cyclohexane The ratio of ketone and terpineol is 70:30), and it is made into inkjet ink, and the viscosity is adjusted to 15mPa·s and the surface tension is 35mNm -1 ; Inject the ink into the ink cartridge, and deposit it on the pre-treated PI substrate according to the predetermined pattern using conventional inkjet printing technology; dry the conductive film deposited on the substrate in an oven, and heat-treat at 250°C for 30 minutes to form graphite vinyl conductive film.
[0028]...
Embodiment 3
[0030] Take 80ml of ethanol and 20ml of dimethylformamide and mix them, add 1.5g of ethyl cellulose, take 4g of graphite and add it to ethyl cellulose (EC) / ethanol / dimethylformamide organic solvent; ultrasonic treatment for 80 minutes, Power 150W, temperature 4-6°C; high-speed centrifugation at 10,000 rpm for 60 minutes, take the upper layer liquid, add 40ml NaCl aqueous solution (0.05g / ml) for flocculation, and obtain graphene powder after filtration; disperse the graphene powder in an organic solvent (ring The ratio of hexanone to terpineol is 85:15), and it is made into inkjet ink, and the viscosity is adjusted to 12mPa·s, and the surface tension is 30mNm -1 ;Inject the ink into the ink cartridge, and deposit it on the pre-treated PET substrate according to the predetermined pattern using conventional inkjet printing technology; dry the conductive film deposited on the substrate in an oven, and heat-treat at 200°C for 30 minutes to form graphite vinyl conductive film.
[0...
PUM
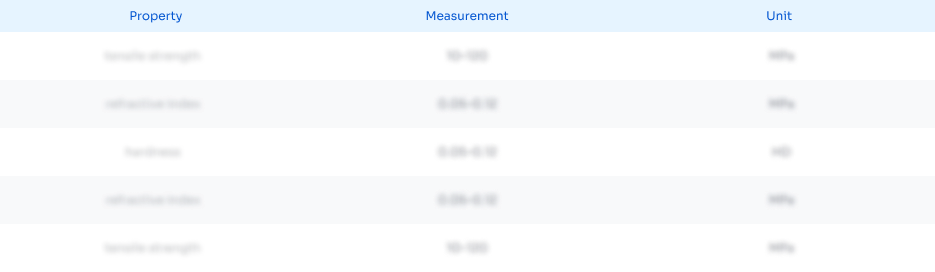
Abstract
Description
Claims
Application Information

- R&D
- Intellectual Property
- Life Sciences
- Materials
- Tech Scout
- Unparalleled Data Quality
- Higher Quality Content
- 60% Fewer Hallucinations
Browse by: Latest US Patents, China's latest patents, Technical Efficacy Thesaurus, Application Domain, Technology Topic, Popular Technical Reports.
© 2025 PatSnap. All rights reserved.Legal|Privacy policy|Modern Slavery Act Transparency Statement|Sitemap|About US| Contact US: help@patsnap.com