Preparation method of phenolic resin
A technology of phenolic resin and phenolic compound, which is applied in the field of preparation of phenolic resin, can solve the problems of non-hardness, high emulsion toughness, and low strength, and achieve the effect of solving the influence of resin color, prolonging the use time, and improving usability
- Summary
- Abstract
- Description
- Claims
- Application Information
AI Technical Summary
Problems solved by technology
Method used
Image
Examples
preparation example Construction
[0026] The invention discloses a preparation method of phenolic resin, comprising the following steps:
[0027] A) under the action of a basic catalyst, the phenolic compound, the aldehyde compound, the reducing agent and the boron-containing compound are subjected to a first reaction to obtain a reaction mixture;
[0028] B) performing a second reaction on the reaction mixture obtained in the above step A) with a nitrogen-containing compound to obtain a phenolic resin.
[0029] In the present invention, under the action of the basic catalyst, the phenolic compound, the aldehyde compound, the reducing agent and the boron-containing compound are subjected to the first reaction to obtain a reaction mixture, and then the second reaction is carried out with the nitrogen-containing compound to obtain the phenolic resin. In the present invention, during the phenolic reaction process, specific proportions of boron-containing compounds, reducing compounds and nitrogen-containing compo...
Embodiment 1
[0048] First, put 1000kg of phenol, 450kg of formaldehyde solution with a mass concentration of 37%, and 9kg of sodium borohydride into the reaction kettle and mix them evenly, then add 30kg of sodium hydroxide, heat up to 60°C, and react at constant temperature for 2 hours, then add 18kg of four The sodium borate was then heated to 70° C., and the constant temperature reaction was continued for 2 hours to obtain a reaction mixture.
[0049] After mixing the above reaction mixture with 25kg of ethylenediamine, react at a temperature of 80°C. When the viscosity of the reaction product is 600cp / 25°C, stop the reaction, and then carry out vacuum distillation. When the reaction product of the above steps When the water content in the medium is 3%, stop the vacuum distillation and add 500kg of methanol. After the product obtained in the above steps is completely dissolved, the temperature is finally lowered to 35°C to obtain light-colored thermosetting phenolic resin 1#.
Embodiment 2
[0051] First, put 1000kg of phenol, 800kg of formaldehyde solution with a mass concentration of 37%, and 12kg of lithium aluminum hydride into the reactor and mix them evenly, then add 20kg of potassium hydroxide, heat up to 66°C, and react at constant temperature for 2 hours, then add 15kg of boric acid Then the temperature was raised to 75° C., and the constant temperature reaction was continued for 2 hours to obtain a reaction mixture.
[0052] After mixing the above reaction mixture with 25kg urea, react at a temperature of 80°C. When the viscosity value of the reaction product is 800cp / 25°C, stop the reaction, and then carry out vacuum distillation. When the reaction product of the above steps contains moisture When the content is 5%, stop the vacuum distillation and add 600kg of acetone. After the product obtained in the above steps is completely dissolved, the temperature is finally lowered to 35°C to obtain light-colored thermosetting phenolic resin 2#.
PUM
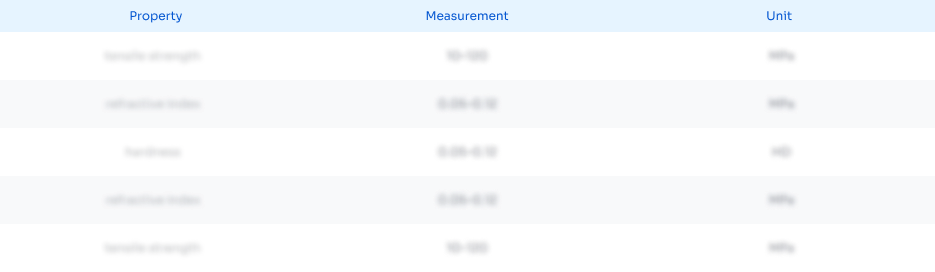
Abstract
Description
Claims
Application Information

- Generate Ideas
- Intellectual Property
- Life Sciences
- Materials
- Tech Scout
- Unparalleled Data Quality
- Higher Quality Content
- 60% Fewer Hallucinations
Browse by: Latest US Patents, China's latest patents, Technical Efficacy Thesaurus, Application Domain, Technology Topic, Popular Technical Reports.
© 2025 PatSnap. All rights reserved.Legal|Privacy policy|Modern Slavery Act Transparency Statement|Sitemap|About US| Contact US: help@patsnap.com