Method for modifying epoxy resin by using amphiphilic copolymer modified graphene
A technology of graphene modification and epoxy resin, which is applied in the preparation of graphene/epoxy resin composite materials, the surface modification and dispersion of graphene, which can solve the problem of graphene's easy aggregation and poor dispersion performance, and its inability to exert its superiority Performance and other issues, to achieve the effect of easy mass production, high yield, and wide process window
- Summary
- Abstract
- Description
- Claims
- Application Information
AI Technical Summary
Problems solved by technology
Method used
Image
Examples
Embodiment 1
[0015] In the first step, stir and dissolve 0.5g of glycidyl methacrylate, 0.5g of vinyl carbazole, and 0.01g of azobisisobutyronitrile in 20mL of tetrahydrofuran, and pass through N 2 5min-30min, sealed, reacted at 70°C for 12h, precipitated after the reaction, dried in a vacuum oven at 20-80°C to obtain the amphiphilic copolymer.
[0016] In the second step, 0.1 g of graphene oxide and 1 g of amphiphilic copolymer were dispersed in tetrahydrofuran, hydrazine hydrate was added, reacted at 70 ° C for 12 h, cooled and centrifuged, and black powder was obtained after drying, which was amphiphilic copolymer modified graphene.
[0017] In the third step, the amphiphilic copolymer modified graphene is finally added to the bisphenol A epoxy resin (E51), decompressed and pumped, and the hexahydrophthalic anhydride curing agent is added to mix evenly and then poured into the mold, wherein the epoxy resin , curing agent and amphiphilic polymer-modified graphene in a weight ratio of 100...
Embodiment 2
[0019] In the first step, stir and dissolve 0.5g glycidyl methacrylate, 1g vinyl carbazole, and 0.015g azobisisobutyronitrile in 20mL tetrahydrofuran, pass N 2 5min-30min, sealed, reacted at 70°C for 12h, precipitated after the reaction, dried in a vacuum oven at 20-80°C to obtain the amphiphilic copolymer.
[0020] In the second step, 0.1 g of graphene oxide and 0.5 g of amphiphilic copolymer were dispersed in tetrahydrofuran, hydrazine hydrate was added, reacted at 70 ° C for 12 h, cooled and centrifuged, and black powder was obtained after drying, which was amphiphilic copolymer modified graphene.
[0021] In the third step, the amphiphilic copolymer modified graphene is finally added to the bisphenol A epoxy resin (E51), decompressed and pumped, and the tetrahydrophthalic anhydride curing agent is added to mix evenly and then poured into the mold, wherein the epoxy resin , curing agent and amphiphilic polymer-modified graphene in a weight ratio of 100:95:1, fully mixed and...
Embodiment 3
[0023] In the first step, stir and dissolve 0.5g glycidyl methacrylate, 1g vinyl carbazole, and 0.015g azobisisobutyronitrile in 20mL tetrahydrofuran, pass N 2 5min-30min, sealed, reacted at 70°C for 12h, precipitated after the reaction, dried in a vacuum oven at 20-80°C to obtain the amphiphilic copolymer.
[0024] In the second step, 0.1 g of graphene oxide and 0.5 g of amphiphilic copolymer were dispersed in tetrahydrofuran, hydrazine hydrate was added, reacted at 70 ° C for 12 h, cooled and centrifuged, and black powder was obtained after drying, which was amphiphilic copolymer modified graphene.
[0025] In the third step, the amphiphilic copolymer modified graphene is finally added to the bisphenol A epoxy resin (E51), decompressed and pumped, and the hexahydrophthalic anhydride curing agent is added to mix evenly and then poured into the mold, wherein the epoxy resin , curing agent and amphiphilic polymer-modified graphene in a weight ratio of 100:95:0.5, fully mixed an...
PUM
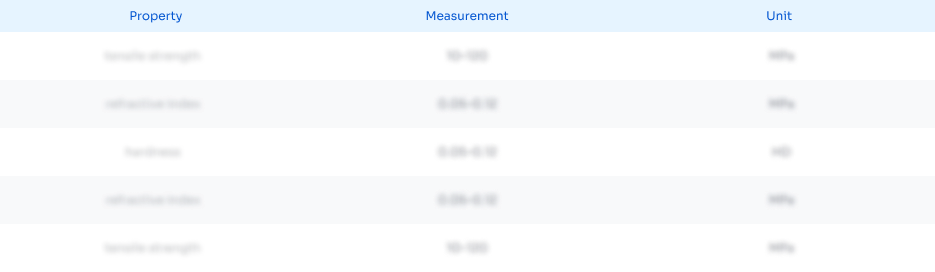
Abstract
Description
Claims
Application Information

- R&D Engineer
- R&D Manager
- IP Professional
- Industry Leading Data Capabilities
- Powerful AI technology
- Patent DNA Extraction
Browse by: Latest US Patents, China's latest patents, Technical Efficacy Thesaurus, Application Domain, Technology Topic, Popular Technical Reports.
© 2024 PatSnap. All rights reserved.Legal|Privacy policy|Modern Slavery Act Transparency Statement|Sitemap|About US| Contact US: help@patsnap.com