Foamable rubber particles
A technology of rubber particles and foaming agent, applied in the field of high molecular polymers, can solve the problems of high energy consumption, high production cost, poor fluidity of rubber materials, etc., and achieve the effects of controllable physical properties, low production cost and soft texture
- Summary
- Abstract
- Description
- Claims
- Application Information
AI Technical Summary
Problems solved by technology
Method used
Examples
Embodiment 1
[0018] Polychloroprene 50 parts
[0019] Standard natural rubber 15 parts
[0020] Ethylene-vinyl acetate copolymer 20 parts
[0021] POE elastomer 1 part
[0022] Foaming agent 1 part
[0023] Vulcanizing agent 1 part
[0024] Strengthening agent 10 parts
[0025] Dispersant 0.5 parts
[0026] Modified flow agent 1.5 parts
[0027] This formula is to meet the requirements of products with high wear resistance, high tensile resistance and microcellular foaming. The production steps are: first put the rubber composition, modified flow agent, reinforcing agent, and dispersant into the internal mixer for internal mixing, mix for 12 minutes, add foaming agent and vulcanizing agent, and mix for 5 minutes. The temperature of the internal mixer is 95°C, and then the rubber particles are formed after kneading and extrusion. Put the foamable rubber particles into the station-type injection molding machine, heat and pressurize the rubber particles to make it into a turbulent rub...
Embodiment 2
[0029] Polychloroprene 30 parts
[0030] Standard natural rubber 10 parts
[0031] Ethylene-vinyl acetate copolymer 15 parts
[0032] POE elastomer 10 parts
[0033] EPDM glue 10 parts
[0034] Filler 10 parts
[0035] Foaming agent 2 parts
[0036] Vulcanizing agent 1 part
[0037] Strengthening agent 10 parts
[0038] Dispersant 0.5 parts
[0039] Modified flow agent 1.5 parts
[0040] This formula is to meet the requirements of high elasticity, anti-aging, acid and alkali resistance, and light foaming products, such as building and mechanical sealing products. The production steps are as follows: first put the rubber composition, modified flow agent, reinforcing agent, and dispersant into the internal mixer for internal mixing, mix for 8 minutes, add foaming agent and vulcanizing agent, and mix for 3 minutes. The temperature of the internal mixer is 90°C, and then it is kneaded and extruded into rubber particles. Put the foamable rubber particles into the station-...
Embodiment 3
[0042] Polychloroprene 15 parts
[0043] Ethylene-vinyl acetate copolymer 20 parts
[0044] POE elastomer 15 parts
[0045] EPDM glue 15 parts
[0046] Filler 15 parts
[0047] Foaming agent 5 parts
[0048] Vulcanizing agent 0.5 parts
[0049]Strengthening agent 7.5 parts
[0050] Dispersant 0.5 parts
[0051] Modified flow agent 1.5 parts
[0052] This formula is to meet the requirements of products with high elasticity, high wear resistance and heavy foaming, such as shoe soles and slippers. The production steps are: first put the rubber composition, modified flow agent, reinforcing agent, and dispersant into the internal mixer for internal mixing, mix for 10 minutes, add foaming agent and vulcanizing agent, and mix for 5 minutes. The temperature of the internal mixer is 95°C, and then the rubber particles are formed after kneading and extrusion. Put the foamable rubber particles into the station-type injection molding machine, heat and pressurize the rubber partic...
PUM
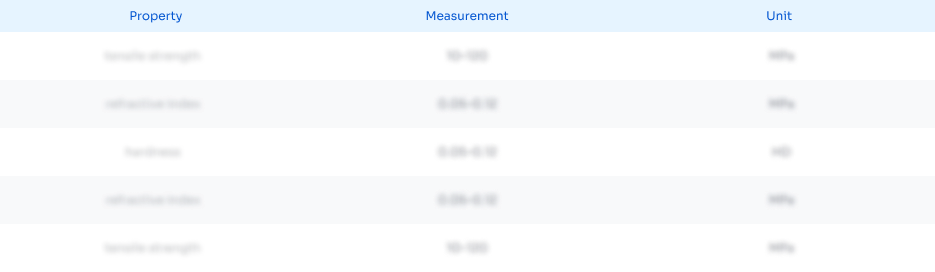
Abstract
Description
Claims
Application Information

- Generate Ideas
- Intellectual Property
- Life Sciences
- Materials
- Tech Scout
- Unparalleled Data Quality
- Higher Quality Content
- 60% Fewer Hallucinations
Browse by: Latest US Patents, China's latest patents, Technical Efficacy Thesaurus, Application Domain, Technology Topic, Popular Technical Reports.
© 2025 PatSnap. All rights reserved.Legal|Privacy policy|Modern Slavery Act Transparency Statement|Sitemap|About US| Contact US: help@patsnap.com