Method for producing clean gasoline
A gasoline and clean technology, used in the petroleum industry, hydrocarbon oil treatment, hydrotreating process, etc., can solve the problems of excessive methanol addition, rapid catalyst deactivation, and inability to achieve maximum conversion of olefins, reducing sulfur content and olefins. The effect of increasing the liquid yield and increasing the content of etherified products
- Summary
- Abstract
- Description
- Claims
- Application Information
AI Technical Summary
Problems solved by technology
Method used
Image
Examples
preparation example 1
[0048] The preparation method of the adsorption and refining catalyst: put a certain amount of diatomite and zinc oxide into a grinder to grind into powder, mix the mixture with deionized water and make a slurry to obtain a slurry with a solid content of 30wt%, and then add a certain amount of aluminum sol, and adjust the pH value to about 3 with hydrochloric acid, then stir at 75°C for 2.5h, cool down to 60°C, and spray-dry to shape; after drying at 150°C for 4 hours, bake at 650°C for 2h to make a carrier; The granules are impregnated with a nickel nitrate solution to produce an impregnated granule mixture; the impregnated granule mixture is dried at 150°C for 2 hours, then calcined at 600°C for 2 hours, and then pressed into tablets to form 1-3mm granules to obtain Adsorption of refined catalysts. Among them: the weight ratio of diatomite, aluminum sol, zinc oxide and nickel nitrate is SiO 2 :Al 2 o 3 : ZnO: Ni=2:1:5:1.
Embodiment 1
[0054] Example 1 illustrates the effect of a method for producing clean gasoline provided by the present invention.
[0055] Attached image 3 The procedure shown was tested. The whole distillate gasoline first enters the refining reactor for desulfurization and dediene under the condition of hydrogen, and then enters the fractionating tower for fractionation into light gasoline fraction and heavy gasoline fraction. After the light gasoline fraction is washed with water, it enters the etherification reactor and reacts with alcohol to form etherified gasoline , the excess methanol enters the methanol extraction tower to recover methanol. The etherified light gasoline fraction and the heavy gasoline fraction are mixed to obtain a clean gasoline product.
[0056] Gasoline raw material is the same as Comparative Example 1. The refining reactor is filled with the adsorption refining catalyst prepared in Preparation Example 1, and the operating conditions are: the reaction temper...
Embodiment 2
[0058] Example 1 illustrates the effect of a method for producing clean gasoline provided by the present invention.
PUM
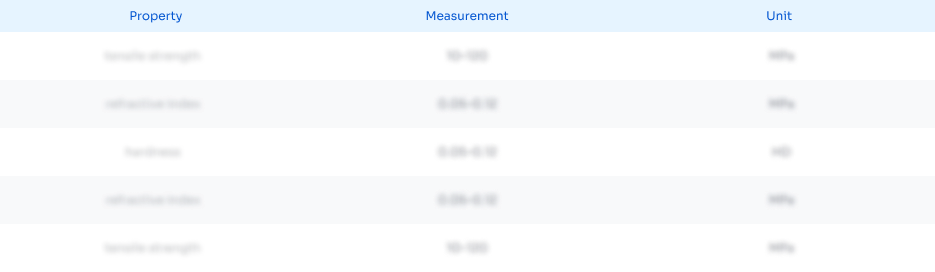
Abstract
Description
Claims
Application Information

- Generate Ideas
- Intellectual Property
- Life Sciences
- Materials
- Tech Scout
- Unparalleled Data Quality
- Higher Quality Content
- 60% Fewer Hallucinations
Browse by: Latest US Patents, China's latest patents, Technical Efficacy Thesaurus, Application Domain, Technology Topic, Popular Technical Reports.
© 2025 PatSnap. All rights reserved.Legal|Privacy policy|Modern Slavery Act Transparency Statement|Sitemap|About US| Contact US: help@patsnap.com