Hot pressure casting moulding method of laser pumping cavity Al2O3 ceramic reflector
A reflector and pump cavity technology, applied in the field of ceramic precision molding, can solve the problems of affecting laser life, poor stability, low thermal conductivity, etc., and achieve the effects of easy control, improved product performance, and simple process
- Summary
- Abstract
- Description
- Claims
- Application Information
AI Technical Summary
Problems solved by technology
Method used
Examples
Embodiment
[0022] First, the premixed Al-containing 2 o 3 The slurry of ceramic powder, paraffin and surfactant is injected into the molding mold at 60°C with a pressure of 7MPa, demolded, and the green body is properly trimmed. Then use the low-temperature degreasing system to remove paraffin and other organic matter by heating from room temperature to 120°C for 12 hours, 120°C to 160°C for 68 hours, and 160°C to 280°C for 48 hours. Finally, the temperature was raised to 1140° C. for calcination at a heating rate of 40° C. / hour, and kept for 2 hours to obtain ceramic products.
[0023] Prepared as described above.
[0024] Al with regular shape and smooth surface can be obtained 2 o 3 Ceramic reflector.
PUM
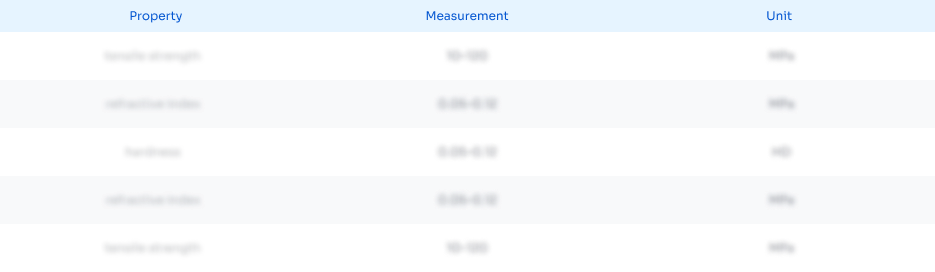
Abstract
Description
Claims
Application Information

- Generate Ideas
- Intellectual Property
- Life Sciences
- Materials
- Tech Scout
- Unparalleled Data Quality
- Higher Quality Content
- 60% Fewer Hallucinations
Browse by: Latest US Patents, China's latest patents, Technical Efficacy Thesaurus, Application Domain, Technology Topic, Popular Technical Reports.
© 2025 PatSnap. All rights reserved.Legal|Privacy policy|Modern Slavery Act Transparency Statement|Sitemap|About US| Contact US: help@patsnap.com