Method for reworking surface defect on back surface of weld joint of small container
A small, back-side technology, applied in household containers, welding equipment, arc welding equipment, etc., can solve the problems of increased rework workload, heavy workload, and long time-consuming rework, so as to reduce the risk of secondary rework and reduce the risk of secondary rework. The risk of rework is small and the effect of reducing the workload of rework
- Summary
- Abstract
- Description
- Claims
- Application Information
AI Technical Summary
Problems solved by technology
Method used
Image
Examples
Embodiment Construction
[0020] Attached below figure 1 and 2 The method for repairing the surface defects on the back of the weld seam of a small container with observation holes and welding holes on the wall of the present invention will be described in detail.
[0021] Such as figure 1 and 2 As shown, when repairing the surface defects on the back of the welding seam of a small oblong vessel with five through holes on the wall, one of the five through holes is selected as the observation hole, and the remaining Choose any one of the four through holes as the soldering hole. For example, when repairing and welding the surface defect on the back of the weld A2, any one of the through hole 21 on the head 2 located at the left end of the small container and the through holes 11a, 11b and 12 located on the cylinder 1 can be selected. Through hole is as observation hole, is as welding hole with the through hole 21 on the sealing head 2 that is positioned at this small container right-hand side. Like...
PUM
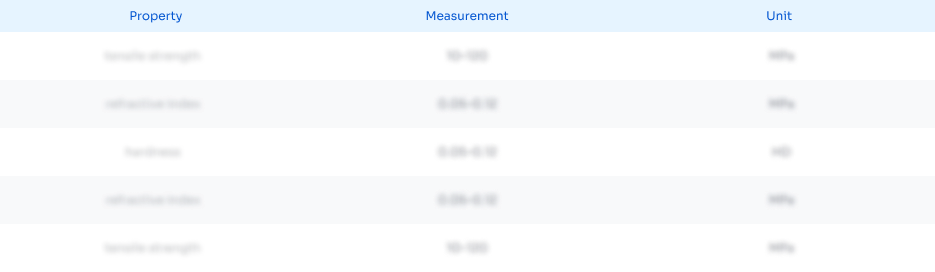
Abstract
Description
Claims
Application Information

- R&D Engineer
- R&D Manager
- IP Professional
- Industry Leading Data Capabilities
- Powerful AI technology
- Patent DNA Extraction
Browse by: Latest US Patents, China's latest patents, Technical Efficacy Thesaurus, Application Domain, Technology Topic, Popular Technical Reports.
© 2024 PatSnap. All rights reserved.Legal|Privacy policy|Modern Slavery Act Transparency Statement|Sitemap|About US| Contact US: help@patsnap.com