Friction press mould base and mould structure
A technology of friction presses and mold bases, applied in forging/pressing/hammering machinery, manufacturing tools, forging/pressing/hammer devices, etc., which can solve problems such as long processing period, large space occupied by mold storage, and many mold materials , achieve the effect of shortening the replacement time, shortening the production cycle, and easy operation
- Summary
- Abstract
- Description
- Claims
- Application Information
AI Technical Summary
Problems solved by technology
Method used
Image
Examples
Embodiment Construction
[0007] Depend on figure 1 As we know, the mold frame and mold structure of the friction press, the upper mold frame and the lower mold frame are set at the two ends of the mold base and can be adjusted freely, and there is a clamping iron clamping round mold in the middle, and the clamping iron clamping round mold is composed of two symmetrical middle Die 1 and mold 2 are formed with semicircular mold holes, and the size of the mold holes is adjusted by bolts and wedges on the upper mold base and the lower mold base.
[0008] The improvement of the upper and lower mold bases of the above graphics, after two years of verification of the mold bases of the four friction presses in our factory, the effect is as follows: After the mold shape is standardized, the mold machining is standardized, and the mold production cycle is shortened (in Based on semi-finished molds), improve the timely supply of molds.
[0009] 1. Realize the multi-purpose of one equipment and one mold base.
...
PUM
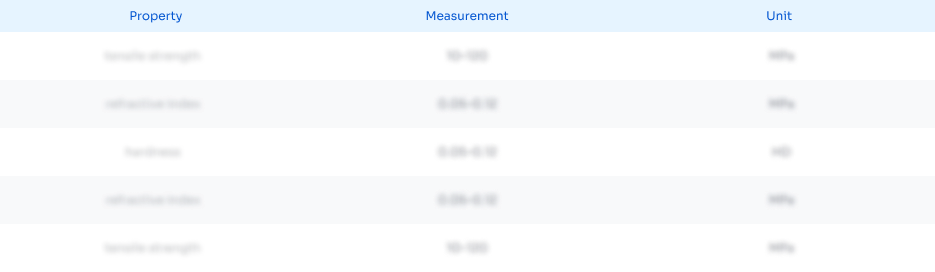
Abstract
Description
Claims
Application Information

- Generate Ideas
- Intellectual Property
- Life Sciences
- Materials
- Tech Scout
- Unparalleled Data Quality
- Higher Quality Content
- 60% Fewer Hallucinations
Browse by: Latest US Patents, China's latest patents, Technical Efficacy Thesaurus, Application Domain, Technology Topic, Popular Technical Reports.
© 2025 PatSnap. All rights reserved.Legal|Privacy policy|Modern Slavery Act Transparency Statement|Sitemap|About US| Contact US: help@patsnap.com