Plastic pipe fitting with plastic-steel composite reinforced threaded insert and its production process
A technology of composite reinforcement and plastic pipe fittings, which is applied in the direction of pipes/pipe joints/fittings, pipe connection layout, mechanical equipment, etc., which can solve the problems of large differences in linear expansion coefficient and thermal conductivity, high material costs and sorting and recycling costs, Pressure and high temperature fluid leakage and other problems, to achieve good corrosion resistance, improve the ability to adapt to high pressure and high temperature occasions, and high material utilization.
- Summary
- Abstract
- Description
- Claims
- Application Information
AI Technical Summary
Problems solved by technology
Method used
Image
Examples
Embodiment Construction
[0072] The present invention will be further described below with specific embodiment, see figure 1 —41:
[0073] Plastic pipe fittings with plastic-steel composite reinforced threaded inserts, including an internal thread sleeve 2 or an external thread sleeve 1 made of thin-walled pipe metal profiles, and a plastic outer coating reinforcement sleeve 5 is formed outside the internal thread sleeve 2 to form a composite reinforcement type internally threaded insert 3 with internal thread; or a plastic inner coating reinforcing sleeve 6 is molded in the externally threaded sleeve 1 to form a composite reinforced externally threaded insert 4 with externally threaded, said internally threaded insert 3 Or one side of the external thread insert 4 is injection-molded with a pipe fitting connection part to form a plastic pipe fitting. External thread cover 1 and internal thread cover 2 are stainless steel thread cover and stainless steel external thread cover. Made of stainless steel...
PUM
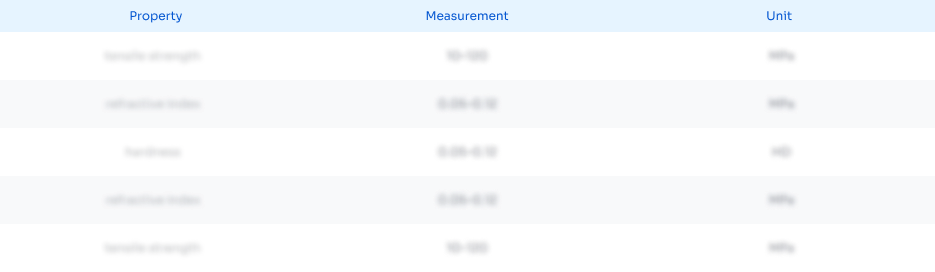
Abstract
Description
Claims
Application Information

- R&D
- Intellectual Property
- Life Sciences
- Materials
- Tech Scout
- Unparalleled Data Quality
- Higher Quality Content
- 60% Fewer Hallucinations
Browse by: Latest US Patents, China's latest patents, Technical Efficacy Thesaurus, Application Domain, Technology Topic, Popular Technical Reports.
© 2025 PatSnap. All rights reserved.Legal|Privacy policy|Modern Slavery Act Transparency Statement|Sitemap|About US| Contact US: help@patsnap.com