Spinning-grade polyoxymethylene material and preparation method thereof
A polyoxymethylene material, spinning grade technology, applied in the field of polymer engineering plastics, can solve the problems of primary fiber stretch limit, performance impact, high cost, etc., to achieve good dispersion and fluidity, strength/elastic modulus improvement, The effect of easy operation of the production process
- Summary
- Abstract
- Description
- Claims
- Application Information
AI Technical Summary
Problems solved by technology
Method used
Image
Examples
preparation example Construction
[0028] The spinning-grade polyoxymethylene material and its preparation method of the present embodiment, the spinning-grade polyoxymethylene material is formed by melting and extruding the following raw materials, and the raw materials include the following components by weight: 100 parts of polyoxymethylene resin polymer, antioxidant 0.01-3 parts, 0.01-7 parts of formaldehyde absorbent, 0.05-5 parts of lubricant; by optimizing and adjusting the formula of additives for the base material, including lubricants, antioxidants, formaldehyde absorbents and other additive formulas The adjustment ensures the dispersibility and fluidity, avoids the problems of frequent stress concentration points and fiber breakage in the fiber, and ensures the spinnability of the material in the spinning process, so that the industrial production of the present invention can be guaranteed;
[0029] When the amount of antioxidant was less than 0.01 parts by weight, the thermal stability of the polyoxy...
Embodiment 9
[0092] Select the polyoxymethylene resin polymer raw material in the preparation embodiment 1 to obtain the polyoxymethylene fiber base material through melt extrusion and post-treatment according to the formula of embodiment 4;
[0093] The polyoxymethylene fiber base material was dried in a vacuum drying oven for 8 hours, melted in a single-screw extruder, and extruded by a melt metering pump, and the extruded melt was filtered and extruded through a 0.5mm die hole. Out; the extruded molten resin is wound up through the winding drum to obtain primary fibers.
[0094] The primary fiber is wound on the upper roll (120°C) for preheating, then passed through the hot clamp (140°C) and then wound on the lower roll (150°C), by controlling the wires that are wound into the roll and out of the roll The speed is used to control the stretching ratio, and the copolymerized polyoxymethylene resin fiber is obtained after the primary fiber is stretched.
[0095] The polyoxymethylene resin...
Embodiment 10
[0098] The process of embodiment ten to embodiment fifteen is exactly the same as embodiment nine, the only difference is that the copolyoxymethylene resin powder corresponding to embodiment ten is derived from preparation embodiment two, and embodiment eleven corresponds to preparation embodiment three and embodiment twelve Corresponding to Preparation Example 4, Example 13 corresponds to Preparation Example 5, Example 14 corresponds to Preparation Example 6, and Example 15 corresponds to Preparation Example 7.
[0099] The technological process of above-mentioned embodiment sees Table 5 and Table 6:
[0100] Table 5 embodiment pellet extrusion parameter
[0101]
[0102] Table 6 embodiment primary fiber extrusion parameters
[0103]
PUM
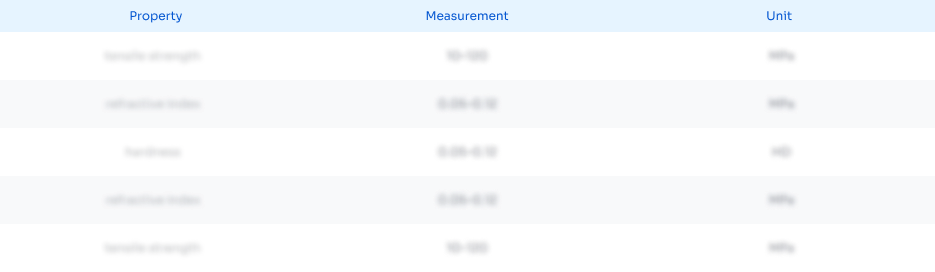
Abstract
Description
Claims
Application Information

- R&D Engineer
- R&D Manager
- IP Professional
- Industry Leading Data Capabilities
- Powerful AI technology
- Patent DNA Extraction
Browse by: Latest US Patents, China's latest patents, Technical Efficacy Thesaurus, Application Domain, Technology Topic, Popular Technical Reports.
© 2024 PatSnap. All rights reserved.Legal|Privacy policy|Modern Slavery Act Transparency Statement|Sitemap|About US| Contact US: help@patsnap.com