Preparation method of strengthened polycrystalline cubic boron nitride composite super-hard material
A technology of cubic boron nitride and superhard material is applied in the synthesis field of polycrystalline cubic boron nitride composite superhard material to achieve the effect of broadening the application field
- Summary
- Abstract
- Description
- Claims
- Application Information
AI Technical Summary
Problems solved by technology
Method used
Image
Examples
Embodiment 1
[0028] 1. Use a laser cutting machine to cut cubic boron carbonitride into small square columns of 1×1×4mm.
[0029] 2. Powder configuration:
[0030] Proportion cBN according to the proportion of particle size of 1-2μm, 5-10μm, 20-30μm and its mass proportion is 15%, 25% and 60% respectively; Purify cBN, first carry out alkali treatment and then carry out acid treatment; Alkali treatment is to mix solid NaOH or KOH with cBN according to the weight ratio of 1:1, put it into a muffle furnace, keep it warm at 350°C for 1 hour, and then rinse it with hot water until neutral; acid treatment is to mix alkali Pour the treated cBN into a large volume beaker, add nitric acid 2-3cm higher than cBN and boil for 20 minutes, pour off the nitric acid, add more hydrochloric acid and boil for 20 minutes, wash with distilled water until neutral.
[0031] Al and Al 2 o 3 , SiC is mixed according to the weight ratio of 2:1:1 as an adhesive, and the adhesive is mechanically treated in a vacuu...
Embodiment 2
[0036] 1. Use a laser cutting machine to cut boron carbide into small cylinders of Φ1×4mm.
[0037] 2. Powder configuration:
[0038] Proportion cBN according to the proportion of particle size of 1-2μm, 5-10μm, 20-30μm and its mass proportion is 10%, 30% and 60% respectively; Purify cBN, first carry out alkali treatment and then carry out acid treatment; Alkali treatment is to mix solid NaOH or KOH with cBN according to the weight ratio of 1:1, put it into a muffle furnace, keep it warm at 350°C for 1 hour, and then rinse it with hot water until neutral; acid treatment is to mix alkali Pour the treated cBN into a large volume beaker, add nitric acid 2-3cm higher than cBN and boil for 20 minutes, pour off the nitric acid, add more hydrochloric acid and boil for 20 minutes, wash with distilled water until neutral.
[0039] Mixing Al and SiC in a ratio of 1:1 as a binder, the binder is mechanically treated in a vacuum ball mill, and ball milled for 48h;
[0040] Mix cBN and ad...
Embodiment 3
[0044] 1. Use a laser cutting machine to cut nano-twinned cubic boron nitride into triangular prisms with a side length of 1.2mm and a height of 4mm;
[0045] 2. Powder configuration:
[0046] Proportion cBN according to the proportion of particle size 1-2μm, 5-10μm, 20-30μm and its mass proportion is 12%, 32% and 56% respectively; Purify cBN, first carry out alkali treatment and then carry out acid treatment; Alkali treatment is to mix solid NaOH or KOH with cBN according to the weight ratio of 1:1, put it into a muffle furnace, keep it warm at 350°C for 1 hour, and then rinse it with hot water until neutral; acid treatment is to mix alkali Pour the treated cBN into a large volume beaker, add nitric acid 2-3cm higher than cBN and boil for 20 minutes, pour off the nitric acid, add more hydrochloric acid and boil for 20 minutes, wash with distilled water until neutral.
[0047] Al, Ti and SiC, Al 4 N 3 According to the weight ratio of 1: 1: 1: 1, it is mixed as an adhesive, ...
PUM
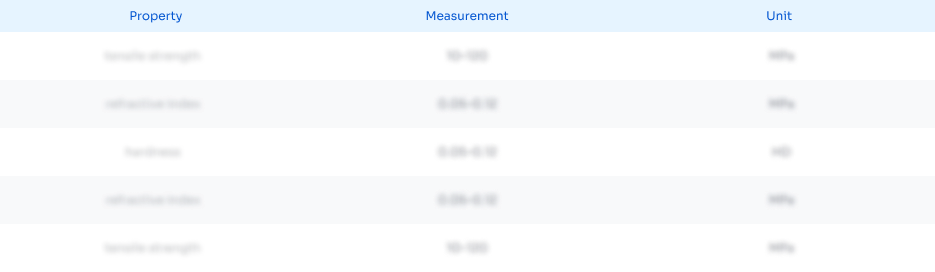
Abstract
Description
Claims
Application Information

- R&D Engineer
- R&D Manager
- IP Professional
- Industry Leading Data Capabilities
- Powerful AI technology
- Patent DNA Extraction
Browse by: Latest US Patents, China's latest patents, Technical Efficacy Thesaurus, Application Domain, Technology Topic, Popular Technical Reports.
© 2024 PatSnap. All rights reserved.Legal|Privacy policy|Modern Slavery Act Transparency Statement|Sitemap|About US| Contact US: help@patsnap.com