Cement-based composite foam insulation board and preparation method thereof
A technology of composite foaming and thermal insulation board, which is applied in the field of building thermal insulation materials, can solve the problems of releasing toxic gas, high safety hazard, poor fire rating, etc., and achieve the effects of shortening construction period, reducing manufacturing cost and large construction cost.
- Summary
- Abstract
- Description
- Claims
- Application Information
AI Technical Summary
Problems solved by technology
Method used
Image
Examples
Embodiment 1~ Embodiment 6
[0019] The preparation method of the cement-based composite foam insulation board provided by the present invention comprises the following steps: (1) Raw materials are prepared according to the weight percentage in Table 1. , latex powder, and reinforcing fiber are put into a mixer, add water and stir for 3-5 minutes, the water temperature is controlled at 45-55°C, then add foaming agent and stir for 5-10 seconds at a speed of 131 rpm to obtain a slurry; (2 ) Open the discharge valve, put the slurry into the mold within 3-5 seconds, stop foaming for 5-10 minutes, release the mold after 12 hours with the solidification of the slurry, and cover it with a plastic film for moisturizing and maintenance for 48 hours After cutting and packaging is the finished product.
[0020] Table 1 Component content (percentage by weight) of each embodiment
[0021]
[0022] Table 2 Product performance index value of each embodiment
[0023]
PUM
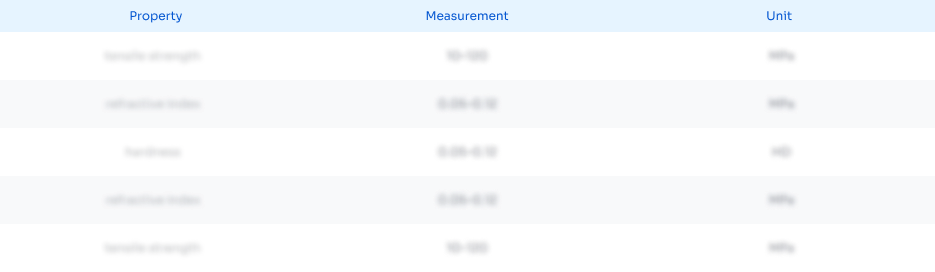
Abstract
Description
Claims
Application Information

- R&D Engineer
- R&D Manager
- IP Professional
- Industry Leading Data Capabilities
- Powerful AI technology
- Patent DNA Extraction
Browse by: Latest US Patents, China's latest patents, Technical Efficacy Thesaurus, Application Domain, Technology Topic, Popular Technical Reports.
© 2024 PatSnap. All rights reserved.Legal|Privacy policy|Modern Slavery Act Transparency Statement|Sitemap|About US| Contact US: help@patsnap.com