Cutting process and device for improving surface brightness of machined metal parts
A metal processing and surface brightness technology, which is applied in metal processing equipment, metal processing machinery parts, measuring/indicating equipment, etc., can solve the problems that the temperature cannot be lowered instantaneously, and the cutting temperature environment cannot be improved, so as to improve the cutting environment and prolong the cutting time. Lifespan, effect of ensuring smoothness
- Summary
- Abstract
- Description
- Claims
- Application Information
AI Technical Summary
Problems solved by technology
Method used
Image
Examples
Embodiment
[0040] Example: see figure 1 , the cutting technology that the present embodiment provides to improve the surface brightness of metal processing parts, it comprises the steps:
[0041] (1) A processing machine tool is provided, and the main shaft of the machine tool is provided with a high-pressure oil mist pipe and a cutter head and a nozzle 6 of the central steam hole;
[0042] (2) Set up a high-pressure oil mist compression device, the high-pressure oil mist compression device includes a coolant storage tank 1 and an air compression pump 2, the high-pressure oil mist compression device is connected to the spindle of the processing machine tool; specifically, it also includes:
[0043] A liquid flow controller 5 is installed in the high-pressure oil mist compression device, which receives the control signal of the controller 7 to adjust the coolant flow;
[0044] A gas flow controller 4 is installed in the high-pressure oil mist compression device, which receives the contro...
PUM
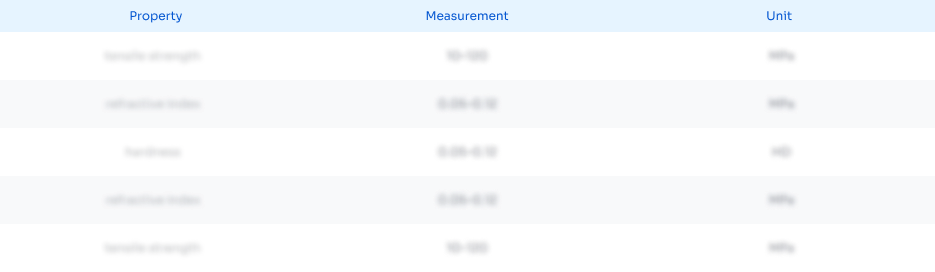
Abstract
Description
Claims
Application Information

- R&D Engineer
- R&D Manager
- IP Professional
- Industry Leading Data Capabilities
- Powerful AI technology
- Patent DNA Extraction
Browse by: Latest US Patents, China's latest patents, Technical Efficacy Thesaurus, Application Domain, Technology Topic, Popular Technical Reports.
© 2024 PatSnap. All rights reserved.Legal|Privacy policy|Modern Slavery Act Transparency Statement|Sitemap|About US| Contact US: help@patsnap.com