Lightweight wall panel superplastic forming production method
A superplastic forming and manufacturing method technology, which is applied in the field of precision sheet metal processing, can solve the problems of difficult shape precision control, poor part integrity, high cost, etc., and achieve the effects of avoiding deformation control problems, improving efficiency, and eliminating residual stress
- Summary
- Abstract
- Description
- Claims
- Application Information
AI Technical Summary
Problems solved by technology
Method used
Image
Examples
specific Embodiment approach
[0025] The specific implementation method is carried out according to the following process steps: the first step is to carry out plane expansion: according to the size of the part, the part is expanded into the same plane, the size of the blank and the position and size of the rib outline are determined, and then the welding position is determined, and the process is appropriately increased Allowance; the second step of blanking: according to the size of the blank after expansion, appropriately increase the process allowance, increase 66mm in the length direction, and increase 59mm in the width direction, see figure 2 , using laser cutting or numerical control punching methods to obtain two blanks with a thickness of 3mm and 2mm respectively; blow slag and deburr the above blanks; the third step of welding: pickling the parts to be welded before welding, and put them in a drying furnace Dry at 90°C to 100°C for 20min to 30min. Grind the welding area with a rotating wire brus...
PUM
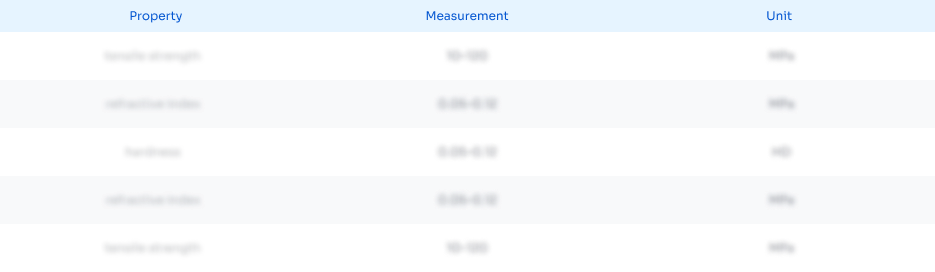
Abstract
Description
Claims
Application Information

- R&D Engineer
- R&D Manager
- IP Professional
- Industry Leading Data Capabilities
- Powerful AI technology
- Patent DNA Extraction
Browse by: Latest US Patents, China's latest patents, Technical Efficacy Thesaurus, Application Domain, Technology Topic, Popular Technical Reports.
© 2024 PatSnap. All rights reserved.Legal|Privacy policy|Modern Slavery Act Transparency Statement|Sitemap|About US| Contact US: help@patsnap.com