Composite type flexible pressure and displacement sensitive element and preparation method thereof
A displacement sensitive and composite technology, applied in the field of measurement, can solve the problems of limited application, inability to realize pressure measurement, inability to complete non-contact displacement measurement, etc., and achieve the effect of saving installation space, thin thickness and high flexibility
- Summary
- Abstract
- Description
- Claims
- Application Information
AI Technical Summary
Problems solved by technology
Method used
Image
Examples
Embodiment 1
[0016]A via hole with a diameter of 300 microns is opened on a polyimide film with a thickness of 12.5 microns, and a copper foil with a thickness of 10 microns is laminated on the front and back surfaces of the polyimide film and the via holes, and the front copper foil is treated. Photolithography, forming a copper foil coil centered on the via hole, forming an edge lead on the end side of the copper foil coil, performing photolithography on the reverse copper foil to form a center lead 5, and then completing the preparation of the displacement sensitive layer, the copper foil The shape of the coil is circular, the number of turns is 50, the line width is 0.15 microns, and the line distance is 0.3 microns. The carbon nanotube powder with an aspect ratio of 100 and polydimethylsiloxane are used in a mass ratio of 0.04:1. mixed, and added to n-hexane to form a carbon nanotube / polydimethylsiloxane / n-hexane mixed solution, and the carbon nanotube / polydimethylsiloxane / n-hexane mix...
Embodiment 2
[0018] A via hole with a diameter of 300 microns is opened on a polyimide film with a thickness of 12.5 microns, and a copper foil with a thickness of 10 microns is laminated on the front and back surfaces of the polyimide film and the via holes, and the front copper foil is treated. Photolithography, forming a copper foil coil centered on the via hole, forming an edge lead on the end side of the copper foil coil, performing photolithography on the reverse copper foil to form a center lead 5, and then completing the preparation of the displacement sensitive layer, the copper foil The shape of the coil is circular, the number of turns is 80, the line width is 0.3 microns, and the line distance is 0.3 microns. Graphene powder with a specific surface area of 50 square meters per gram and polyethylene are mixed in a mass ratio of 0.04:1, and It is added to n-hexane to form a graphene / polyethylene / n-hexane mixed solution, and the graphene / polyethylene / n-hexane mixed solution is su...
Embodiment 3
[0020] A via hole with a diameter of 300 microns is opened on a polyimide film with a thickness of 12.5 microns, and a copper foil with a thickness of 10 microns is laminated on the front and back surfaces of the polyimide film and the via holes, and the front copper foil is treated. Photolithography, forming a copper foil coil centered on the via hole, forming an edge lead on the end side of the copper foil coil, performing photolithography on the reverse copper foil to form a center lead 5, and then completing the preparation of the displacement sensitive layer, the copper foil The shape of the coil is circular, the number of turns is 60, the line width is 0.15 microns, and the line distance is 0.15 microns. Carbon black powder and resin with a specific surface area of 780 square meters per gram are mixed in a mass ratio of 0.06:1, and the It is added to n-hexane to form a carbon black / resin / n-hexane mixed solution, and the carbon black / resin / n-hexane mixed solution is mech...
PUM
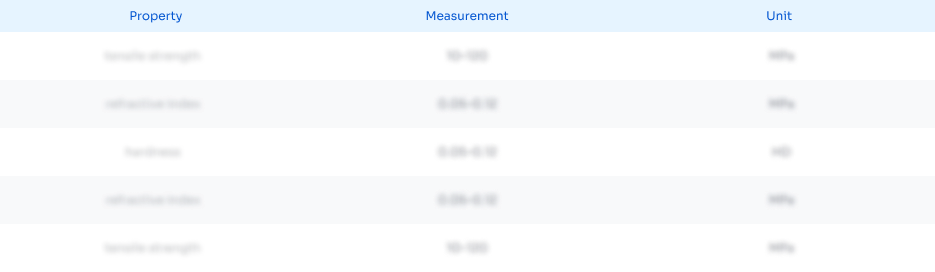
Abstract
Description
Claims
Application Information

- R&D
- Intellectual Property
- Life Sciences
- Materials
- Tech Scout
- Unparalleled Data Quality
- Higher Quality Content
- 60% Fewer Hallucinations
Browse by: Latest US Patents, China's latest patents, Technical Efficacy Thesaurus, Application Domain, Technology Topic, Popular Technical Reports.
© 2025 PatSnap. All rights reserved.Legal|Privacy policy|Modern Slavery Act Transparency Statement|Sitemap|About US| Contact US: help@patsnap.com