Method for preparing high-quality needle coke raw material by removing QI (Quinoline Insolubles) in coal tar
A needle coke raw material, coal tar technology, applied in the direction of only multi-stage serial refining process, etc., can solve the problems of complicated process, expensive price, low yield of solvent method, etc.
- Summary
- Abstract
- Description
- Claims
- Application Information
AI Technical Summary
Problems solved by technology
Method used
Image
Examples
specific Embodiment approach
[0021] The method for removing coal tar QI of the present invention to prepare high-quality needle coke raw material, its preferred embodiment is:
[0022] Include steps:
[0023] First, add the aromatic hydrocarbon solvent and the aliphatic hydrocarbon solvent alone or the mixed solvent after mixing into the raw coal tar, after stirring and gravity sedimentation, the solution is divided into supernatant liquid and residue;
[0024] Afterwards, the supernatant is distilled to obtain refined coal tar with low QI content.
[0025] The aromatic hydrocarbon solvent includes wash oil, and the aliphatic hydrocarbon solvent includes kerosene.
[0026] The mass percentage of the washing oil in the mixed solvent is 1-99%.
[0027] The aromatic hydrocarbon solvent also includes phenanthrene.
[0028] The phenanthrene accounts for 0.1-8% by mass of the raw coal tar, and the mass ratio of the raw coal tar to the mixed solvent is 1:0.8-1:3.
[0029] The gravity settling process is carr...
Embodiment 1
[0039] The basic properties of the raw coal tar used in the experiment are shown in Table 1. Such as figure 1 As shown, take 100g of coal tar, 37.5g of washing oil and 62.5g of kerosene and preheat them in a constant temperature oil bath at 100°C. After sufficient preheating, put the three in the same beaker and mix evenly (also in a constant temperature oil bath at 100°C). After stirring for 30 min, the mixed solution was allowed to stand for 2 h. Take the upper layer in a three-necked flask, and keep the residue for later use. The experimental device such as figure 2 The link shown is fine. Heat the upper layer liquid, observe the liquid phase temperature and gas phase temperature, and ensure that the liquid phase temperature does not exceed 390°C. Finally, refined coal tar is obtained. The yield of refined coal tar was measured to be 66%, and the QI content was 0.24%.
Embodiment 2
[0041] The basic properties of the raw coal tar used in the experiment are shown in Table 1. Such as figure 1 As shown, take 100g of coal tar, 42.9g of washing oil and 107.1g of kerosene and preheat them in a constant temperature oil bath at 100°C. After sufficient preheating, put the three in the same beaker and mix evenly (also in a constant temperature oil bath at 100°C). After stirring for 30 min, the mixed solution was allowed to stand for 2 h. Take the upper layer in a three-necked flask, and keep the residue for later use. The experimental device such as figure 2 The link shown is fine. Heat the upper layer liquid, observe the liquid phase temperature and gas phase temperature, and ensure that the liquid phase temperature does not exceed 390°C. Finally, refined coal tar is obtained. The yield of refined coal tar was measured to be 58%, and the QI content was 0.04%.
PUM
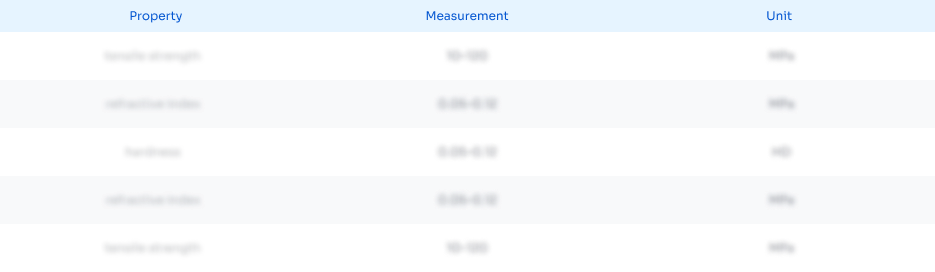
Abstract
Description
Claims
Application Information

- Generate Ideas
- Intellectual Property
- Life Sciences
- Materials
- Tech Scout
- Unparalleled Data Quality
- Higher Quality Content
- 60% Fewer Hallucinations
Browse by: Latest US Patents, China's latest patents, Technical Efficacy Thesaurus, Application Domain, Technology Topic, Popular Technical Reports.
© 2025 PatSnap. All rights reserved.Legal|Privacy policy|Modern Slavery Act Transparency Statement|Sitemap|About US| Contact US: help@patsnap.com