Decorative plastic surface vacuum-coating film preparation method
A vacuum coating and plastic technology, applied in vacuum evaporation coating, sputtering coating, ion implantation coating and other directions, can solve the problems of poor electromagnetic shielding effect, poor industrialization effect, poor material homogeneity, etc. Achieve the effect of promoting rapid development, improving anti-corrosion and moth-eaten ability, and improving strength and wear resistance
- Summary
- Abstract
- Description
- Claims
- Application Information
AI Technical Summary
Problems solved by technology
Method used
Examples
Embodiment Construction
[0023] Sand the plastic, use coarse and fine sandpaper to sand the surface separately, so that a good bonding effect can be obtained, and then put the plastic in hot water at 60°C for 3 minutes of water immersion , the main purpose is to remove dust and some impurities on the surface of the plastic, and remove the hot and cold water extract deposited in the plastic. The plastic extract is made of organic solvents such as ethanol, benzene, ether, acetone, or methylene chloride and The general term for the substances extracted by water to ensure that the plastic has a clean surface and dry naturally after cleaning. Coating melamine formaldehyde resin or aqueous solution on the plastic surface, the melamine formaldehyde resin or aqueous solution contains 1% 3-aminopropyltriethoxysilane coupling agent, 5% lactic acid complexing agent and 10% oxalic acid stabilizer; Seal the plastic. After drying, put it in a washing box containing 1% dilute phosphoric acid to wash off the residua...
PUM
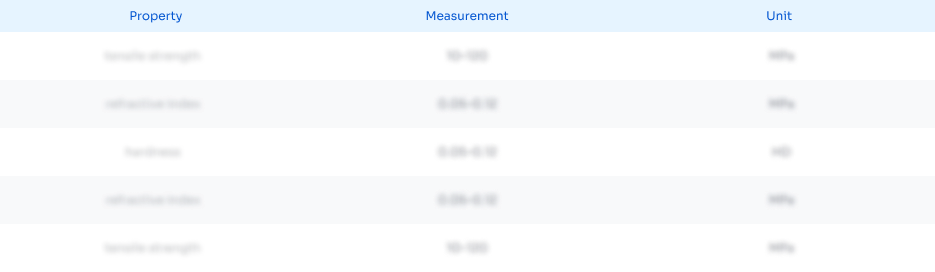
Abstract
Description
Claims
Application Information

- R&D
- Intellectual Property
- Life Sciences
- Materials
- Tech Scout
- Unparalleled Data Quality
- Higher Quality Content
- 60% Fewer Hallucinations
Browse by: Latest US Patents, China's latest patents, Technical Efficacy Thesaurus, Application Domain, Technology Topic, Popular Technical Reports.
© 2025 PatSnap. All rights reserved.Legal|Privacy policy|Modern Slavery Act Transparency Statement|Sitemap|About US| Contact US: help@patsnap.com