Device and method for reducing small casting blank molten steel impact depth
A technology for molten steel and casting billets, which is applied in the field of devices for slowing the impact depth of molten steel in small billets, can solve the problems of reduced service life, increased costs, and reduced flow rate of molten steel, and achieves the effects of uniform temperature, slowing impact depth, and reducing internal stress.
- Summary
- Abstract
- Description
- Claims
- Application Information
AI Technical Summary
Problems solved by technology
Method used
Image
Examples
Embodiment 1
[0026] The specific parameters of the outlet electromagnetic stirrer 1 designed for 120×120mm billet are shown in Table 1.
[0027] Table 1. Parameters of 120×120mm Billet Nozzle Electromagnetic Stirrer
[0028] name parameter Stirrer box inner diameter mm Ф150 Stirrer box outer diameter mm Ф400 Stirrer box height mm 150 power supply Two-phase power Frequency Hz 50 Coil current A 40
[0029] The installation position of the electromagnetic stirrer 1 is as follows: image 3 shown. Because the electromagnetic stirrer 1 needs to be cooled by water, in order to prevent the temperature from dropping too fast near the nozzle, the electromagnetic stirrer 1 can be wrapped with refractory felt or other heat-insulating and high-temperature-resistant materials. Set the current size and frequency of the electromagnetic stirrer 1 before starting casting. Turn on the power supply of the electromagnetic stirrer 1 during ca...
Embodiment 2
[0031] The specific parameters of the outlet electromagnetic stirrer 1 designed for 160×160mm billet are shown in Table 2.
[0032] Table 2. Parameters of 160×160mm Billet Nozzle Electromagnetic Stirrer
[0033] name parameter Stirrer box inner diameter mm Ф180 Stirrer box outer diameter mm Ф450 Stirrer box height mm 160 power supply Three-phase 380V industrial electricity Frequency Hz 30 Coil current A 50
Embodiment 3
[0035] The specific parameters of the nozzle electromagnetic stirrer 1 designed on the Ф150mm round billet are shown in Table 3.
[0036] Table 3. Parameters of Electromagnetic Stirrer at Ф150mm Round Billet Nozzle
[0037] name parameter Stirrer box inner diameter mm Ф160 Stirrer box outer diameter mm Ф420 Stirrer box height mm 150 power supply Three-phase 380V industrial electricity Frequency Hz 100 Coil current A 30
PUM
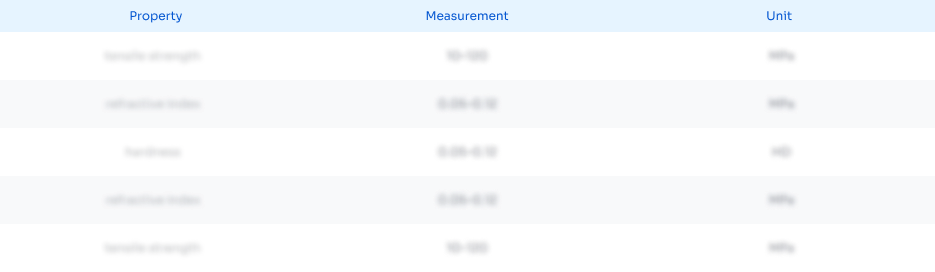
Abstract
Description
Claims
Application Information

- R&D
- Intellectual Property
- Life Sciences
- Materials
- Tech Scout
- Unparalleled Data Quality
- Higher Quality Content
- 60% Fewer Hallucinations
Browse by: Latest US Patents, China's latest patents, Technical Efficacy Thesaurus, Application Domain, Technology Topic, Popular Technical Reports.
© 2025 PatSnap. All rights reserved.Legal|Privacy policy|Modern Slavery Act Transparency Statement|Sitemap|About US| Contact US: help@patsnap.com