Method for removing titanium in molten iron
A technology for detitanium removal and molten iron, which is applied in the manufacture of converters, etc., can solve the problems of unsatisfactory detitanium removal effect and low efficiency of molten iron, and achieve the effect of ensuring the efficiency and stability of detitanium removal
- Summary
- Abstract
- Description
- Claims
- Application Information
AI Technical Summary
Problems solved by technology
Method used
Image
Examples
Embodiment 1
[0022] The initial Ti0.18%, Si0.37%, and Mn0.123% of molten iron before non-oriented electrical steel smelting cannot meet the requirements of Ti≤0.12% for medium-grade non-oriented silicon steel, which may cause the improvement of the finished product and affect the product performance.
[0023] Step: 201: add titanium removal agent to the torpedo tank before tapping in the iron factory, so that on the one hand, the impact of molten iron can be used to remove titanium from the torpedo tank, and the titanium removal reaction can be continued during the process of transporting the molten iron to steelmaking. After steelmaking, the Ti content of molten iron drops to 0.13%. In addition, before ironmaking and tapping, add the detitanium agent in bags into the torpedo tank, and use the waste heat of the torpedo tank to bake before use. After baking for 32 minutes, tap the iron At the same time, the impact of molten iron is used to complete the oxidation reaction of titanium removal ...
Embodiment 2
[0033] The initial Ti0.088%, Si0.47%, and Mn0.14% of molten iron before smelting of non-oriented electrical steel cannot meet the requirement of Ti≤0.06% for medium-grade non-oriented silicon steel, which may cause the improvement of the finished product and affect the product performance.
[0034] Step 301: Add titanium removal agent to the torpedo tank before tapping in the iron factory, so that on the one hand, the impact of molten iron can be used to remove titanium from the torpedo tank, and the titanium removal reaction can be continued during the process of transporting the molten iron to steelmaking. After steelmaking, the Ti content of molten iron is reduced to 0.13%. In addition, before ironmaking and tapping, add the detitanium agent in bags into the torpedo tank, and use the residual heat of the torpedo tank to bake before use. After baking for 32 minutes, when tapping The impact of molten iron is used to complete the oxidation reaction of titanium removal agent and...
PUM
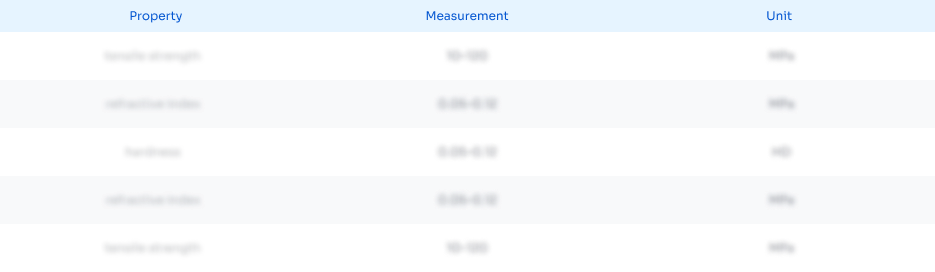
Abstract
Description
Claims
Application Information

- R&D
- Intellectual Property
- Life Sciences
- Materials
- Tech Scout
- Unparalleled Data Quality
- Higher Quality Content
- 60% Fewer Hallucinations
Browse by: Latest US Patents, China's latest patents, Technical Efficacy Thesaurus, Application Domain, Technology Topic, Popular Technical Reports.
© 2025 PatSnap. All rights reserved.Legal|Privacy policy|Modern Slavery Act Transparency Statement|Sitemap|About US| Contact US: help@patsnap.com