Drive system for unit parallel shunting at side of wound rotor motor operating in two quadrants
A transmission system and wire-wound technology, applied in the field of transmission system, can solve the problems of expensive parallel capacitor reactive power compensation equipment, bulky and other problems, and achieve the effect of simple structure, low withstand voltage and high fault tolerance
- Summary
- Abstract
- Description
- Claims
- Application Information
AI Technical Summary
Problems solved by technology
Method used
Image
Examples
Embodiment Construction
[0014] 1. figure 1 An example of the overall structure of the transmission system according to the embodiment of the present invention is given. figure 1 The stator windings in the motor unit 1 are connected to the stator power supplies A, B, and C. The motor rotor winding 2 can be a single or multiple sets of three-phase windings, and the three-phase winding A in the motor rotor winding 2 1 , B 1 、C 1 The rotor current is drawn and connected to the frequency conversion control device 5 through the current extraction unit 3 (which can be a slip ring and a brush or other devices that can extract current), and the frequency conversion control device 5 is connected to the rotor power supply U, V, W; three-phase winding A 2 , B 2 、C 2 The rotor current is connected to the frequency conversion control device 6 through the current extraction unit 4, and the frequency conversion control device 6 is connected to the rotor power supply U, V, W, and so on, and more parallel contro...
PUM
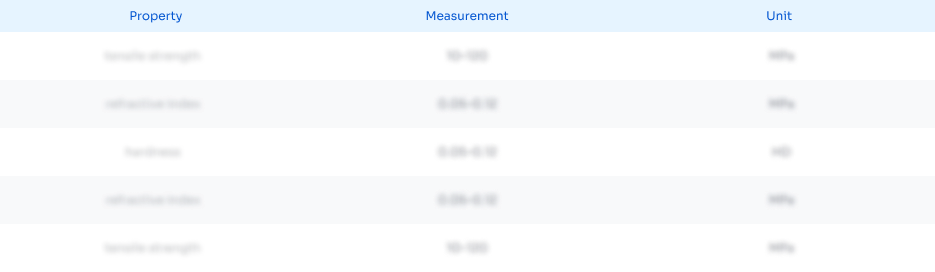
Abstract
Description
Claims
Application Information

- R&D
- Intellectual Property
- Life Sciences
- Materials
- Tech Scout
- Unparalleled Data Quality
- Higher Quality Content
- 60% Fewer Hallucinations
Browse by: Latest US Patents, China's latest patents, Technical Efficacy Thesaurus, Application Domain, Technology Topic, Popular Technical Reports.
© 2025 PatSnap. All rights reserved.Legal|Privacy policy|Modern Slavery Act Transparency Statement|Sitemap|About US| Contact US: help@patsnap.com