Piezoelectric valveless micropump suction cup based on parallel connection compliant mechanism
A compliant mechanism and suction cup technology, applied in the field of special robots, can solve the problems of low power-to-weight ratio, inability to reduce volume and size, and high noise, and achieve the effects of long dynamic period, light weight and low energy consumption.
- Summary
- Abstract
- Description
- Claims
- Application Information
AI Technical Summary
Problems solved by technology
Method used
Image
Examples
Embodiment Construction
[0037] The embodiments of the present invention will be described in detail below in conjunction with the accompanying drawings. This embodiment is implemented on the premise of the technical solution of the present invention, and detailed implementation methods and specific operating procedures are provided, but the protection scope of the present invention is not limited to the following Example.
[0038] Please refer to figure 1 and figure 2, which shows a piezoelectric valveless micropump chuck based on a parallel compliant mechanism, including a single crystal silicon substrate 1 , a copper-based composite film 2 , a compliant mechanism 4 and a piezoelectric stack driver 3 . The center of the top of the compliance mechanism 4 is provided with a deformation displacement input part 43, the center of the bottom part is provided with a deformation displacement output part 44, and the bottom of the compliance mechanism 4 is provided with a positioning groove 45; The stacked...
PUM
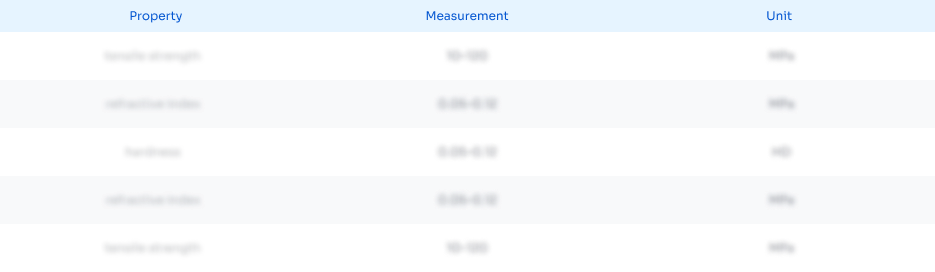
Abstract
Description
Claims
Application Information

- R&D
- Intellectual Property
- Life Sciences
- Materials
- Tech Scout
- Unparalleled Data Quality
- Higher Quality Content
- 60% Fewer Hallucinations
Browse by: Latest US Patents, China's latest patents, Technical Efficacy Thesaurus, Application Domain, Technology Topic, Popular Technical Reports.
© 2025 PatSnap. All rights reserved.Legal|Privacy policy|Modern Slavery Act Transparency Statement|Sitemap|About US| Contact US: help@patsnap.com