Method for recovering pyrite from coal gangue
A technology for coal gangue and pyrite, which is applied in the field of comprehensive utilization of coal gangue, can solve the problems of occupying a large amount of land, environmental pollution, waste of resources, etc., so as to reduce the cost of grinding, reduce environmental pollution, and reduce slagging and adhesion. degree of effect
- Summary
- Abstract
- Description
- Claims
- Application Information
AI Technical Summary
Problems solved by technology
Method used
Image
Examples
Embodiment 1
[0024] The sulfur grade of the ore sample is 9.86% coal gangue, and the specific steps are as follows:
[0025] 1) Crushing: Two-stage crushing by the jaw crusher, and then use a 2mm sieve to check the screening and close-circuit fine crushing of the roller machine to -2mm, and the ore samples crushed to -2mm are mixed by moving piles;
[0026] 2) Grinding: Using imitation closed-circuit grinding, the crushed raw ore is ground to -0.074mm at a grinding concentration of 60%, accounting for 58.83%, and sieved with a 0.043mm sieve to screen out -0.043mm particle size Finally, the +0.043mm particle size returns to the ball mill for regrinding. After three times of grinding, screening, and coarse particle return, the grinding fineness is -0.074mm accounting for 98.58%, and -0.043mm accounting for 95.16%;
[0027] 3) Flotation: rough selection, secondary sweeping, and secondary selection are adopted, and the specific operations are as follows:
[0028] Rough separation: add 50% sul...
Embodiment 2
[0035] The sulfur grade of the ore sample is 5.65% coal gangue, and the specific steps are as follows:
[0036] 1) Crushing: Two-stage crushing by the jaw crusher, and then use a 2mm sieve to check the screening and close-circuit fine crushing of the roller machine to -2mm, and the ore samples crushed to -2mm are mixed by moving piles;
[0037] 2) Grinding: Using imitation closed-circuit grinding, the crushed raw ore is ground to -0.074mm at a grinding concentration of 60%, accounting for 60.65%, and sieved with a 0.043mm sieve to screen out -0.043mm particle size Finally, the +0.043mm particle size returns to the ball mill for regrinding. After three times of grinding, screening, and coarse particle return, the grinding fineness is -0.074mm accounting for 99.15%, and -0.043mm accounting for 95.27%;
[0038] 3) Flotation: rough selection, secondary sweeping, and secondary selection are adopted, and the specific operations are as follows:
[0039] Rough separation: add 50% sul...
PUM
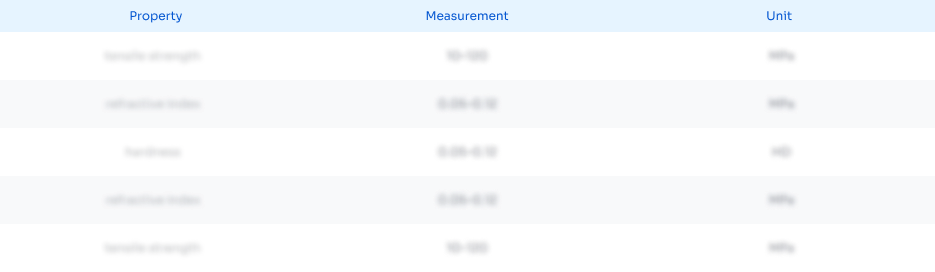
Abstract
Description
Claims
Application Information

- R&D
- Intellectual Property
- Life Sciences
- Materials
- Tech Scout
- Unparalleled Data Quality
- Higher Quality Content
- 60% Fewer Hallucinations
Browse by: Latest US Patents, China's latest patents, Technical Efficacy Thesaurus, Application Domain, Technology Topic, Popular Technical Reports.
© 2025 PatSnap. All rights reserved.Legal|Privacy policy|Modern Slavery Act Transparency Statement|Sitemap|About US| Contact US: help@patsnap.com