A New Method of Reverse Flotation Separation, Grinding and Separation
A new method, the technology of flotation concentrate, applied in flotation, solid separation, etc., can solve the problems of greater influence on the separation effect, influence on production indicators, and increase in tailings grade, so as to reduce the grade of flotation tailings, The effect of improving the grade of flotation concentrate and improving the degree of monomer dissociation
- Summary
- Abstract
- Description
- Claims
- Application Information
AI Technical Summary
Problems solved by technology
Method used
Image
Examples
Embodiment Construction
[0017] The specific implementation manner of the present invention will be described below in conjunction with the accompanying drawings.
[0018] Such as figure 2 As shown, the new method of reverse flotation, ore-centring, grinding and re-election of the present invention comprises one stage of roughing, one stage of fine selection, and three stages of sweeping operations. The tailings of the operation are sent to the first stage of scavenging operation, and the concentrated ore tailings of the first stage of selection are returned to the first stage of roughing operation. The scavenging concentrate (medium ore 2) returns to the first-stage scavenging operation, the tailings are fed into the third-stage scavenging operation, and the concentrate (medium ore 3) selected by the third-stage scavenging operation is returned to the second-stage scavenging operation, which is characterized in that The concentrated ore in the first stage of scavenging operation is regrinded, so th...
PUM
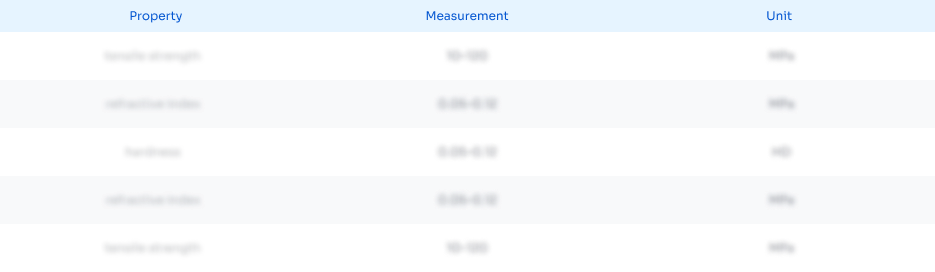
Abstract
Description
Claims
Application Information

- R&D
- Intellectual Property
- Life Sciences
- Materials
- Tech Scout
- Unparalleled Data Quality
- Higher Quality Content
- 60% Fewer Hallucinations
Browse by: Latest US Patents, China's latest patents, Technical Efficacy Thesaurus, Application Domain, Technology Topic, Popular Technical Reports.
© 2025 PatSnap. All rights reserved.Legal|Privacy policy|Modern Slavery Act Transparency Statement|Sitemap|About US| Contact US: help@patsnap.com