Zinc slag reducing agent
A technology of slag reducing agent and total quality, applied in the field of zinc slag reducing agent, can solve the problems of irritating fluorine and chlorine, large smoke and dust, etc., achieve good slagging performance, improve product quality, and good environmental protection and safety effects
- Summary
- Abstract
- Description
- Claims
- Application Information
AI Technical Summary
Problems solved by technology
Method used
Examples
Embodiment 1
[0025] The zinc slag reducing agent S1 of this embodiment is prepared according to the following composition: charcoal powder: 30wt%; sodium nitrate: 10wt%; potassium nitrate: 10wt%; silicon dioxide: 30wt%; calcium carbonate: 10wt%; sodium carbonate: 10wt% .
[0026] Zinc alloys are produced in a coreless induction furnace. When the furnace temperature is about 600°C, the zinc slag reducing agent S1 is used for slagging treatment of zinc alloys. During the slagging process, there is no or less smoke and no irritating odor. The amount of zinc slag reducing agent added is 0.05wt% of the total amount of zinc alloy added to the centerless induction furnace. After slagging treatment, the amount of zinc slag produced by producing 1 ton of zinc alloy is 12 kg, and the direct recovery rate is 98.8%. Ingot, the surface of the ingot is bright without slag inclusion, and the zinc slag produced does not contain fluorine and chlorine.
Embodiment 2
[0028] The zinc slag reducing agent S2 of this embodiment is prepared according to the following composition: charcoal powder: 30wt%; sodium nitrate: 15wt%; potassium nitrate: 5wt%; silicon dioxide: 25wt%; calcium carbonate: 15wt%; sodium carbonate: 10wt% .
[0029] In the production of zinc alloy in a cored induction furnace, when the furnace temperature is about 500°C, use the zinc slag reducing agent S2 to carry out slagging treatment on the zinc alloy liquid. During the slagging process, there is no or less smoke and no irritating smell. produce. The amount of zinc slag reducing agent added is 0.12wt% of the total amount of zinc alloy added to the cored induction furnace. After slagging treatment, the production of 1 ton of zinc alloy produces 18 kg of zinc slag, and the direct recovery rate is 98.2%. Casting into ingots, the surface of the ingots is bright without slag inclusions, and the zinc slag produced does not contain fluorine and chlorine.
Embodiment 3
[0031] The zinc slag reducing agent S3 of this embodiment is prepared according to the following composition: charcoal powder: 20wt%; sodium nitrate: 10wt%; potassium nitrate: 10wt%; silicon dioxide: 30wt%; calcium carbonate: 20wt%; sodium carbonate: 10wt% .
[0032] In a hot-dip galvanizing pot with a capacity of 300 tons, when the temperature of the hot-dip galvanizing alloy solution is 450°C, the zinc slag reducing agent S3 is used for slagging treatment. There is no or less smoke and no irritation during the slagging process. Odor produced. The amount of zinc slag reducing agent added is 0.1wt% of the total amount of hot-dip galvanized alloy in the hot-dip galvanizing pot. After the slagging treatment, the zinc particles contained in the zinc scum are significantly reduced, and the generated zinc slag does not contain fluorine and chlorine, and the floating The total amount of slag is reduced by one-third compared with the prior art, the surface of the galvanized layer is...
PUM
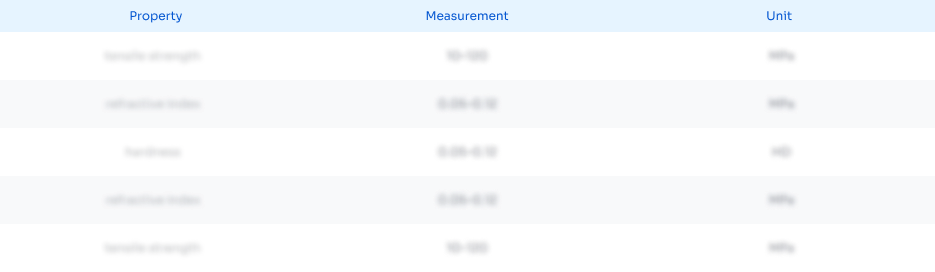
Abstract
Description
Claims
Application Information

- R&D
- Intellectual Property
- Life Sciences
- Materials
- Tech Scout
- Unparalleled Data Quality
- Higher Quality Content
- 60% Fewer Hallucinations
Browse by: Latest US Patents, China's latest patents, Technical Efficacy Thesaurus, Application Domain, Technology Topic, Popular Technical Reports.
© 2025 PatSnap. All rights reserved.Legal|Privacy policy|Modern Slavery Act Transparency Statement|Sitemap|About US| Contact US: help@patsnap.com