Anti-ultraviolet method for cotton fibers
An anti-ultraviolet and cotton fiber technology, applied in fiber treatment, plant fiber, textiles and papermaking, etc., can solve problems such as pollution, affecting the anti-ultraviolet effect of cotton fabrics, affecting the appearance of fabrics, etc.
- Summary
- Abstract
- Description
- Claims
- Application Information
AI Technical Summary
Problems solved by technology
Method used
Image
Examples
Embodiment 1
[0036] According to the above process steps: select 5g of long-staple cotton as the cotton fiber to be treated with UV resistance, weigh 0.25g of butyl titanate and mix with 250ml of absolute ethanol, stir evenly to prepare a sol solution with a concentration of 1g / L, and mix 5g of cotton The fibers were immersed in 150ml of the prepared sol solution, and stood at 20°C for 10min. The cotton fiber after soaking is rolled, and the rolling pressure is 0.2MP. The cotton fibers after padding were subjected to steam treatment under steam at 60°C for 5 min, and washed with clean water. The washed cotton fiber is dried until dry, and the drying temperature is 50°C.
[0037] The long-staple cotton yarn after the anti-ultraviolet treatment of this embodiment was spun and woven, and the ultraviolet protection factor (UPF) of the pure cotton fabric was tested to be 39.1.
Embodiment 2
[0039] According to the above process steps: select 5g of fine-staple cotton as the cotton fiber to be anti-ultraviolet finishing, weigh 0.75g of butyl titanate and mix with 250ml of absolute ethanol, stir evenly to prepare a sol solution with a concentration of 3g / L, and mix 5g of cotton The fibers were immersed in 200ml of the prepared sol solution, and stood at 30°C for 15min. The cotton fiber after soaking is rolled, and the rolling pressure is 0.4MP. The cotton fibers after padding were subjected to steam treatment under steam at 70°C for 7 min, and then washed with water. The cotton fiber after washing is dried to dryness, and the temperature of drying is 60 ℃.
[0040] After the anti-ultraviolet treatment of this embodiment, the fine-staple cotton was spun and woven, and the ultraviolet protection factor (UPF) of the pure cotton fabric was tested to be 43.7.
Embodiment 3
[0042] According to the above process steps: select 5g of long-staple cotton as the cotton fiber to be anti-ultraviolet finishing, weigh 1.5g of butyl titanate and mix with 300ml of absolute ethanol, stir evenly to prepare a sol solution with a concentration of 5g / L, and mix 5g of cotton The fibers were immersed in 250ml of the prepared sol solution, and stood at 40°C for 20min. The soaked cotton fibers are rolled and pressed at a rolling pressure of 0.6MP. The cotton fibers after padding were subjected to steam treatment under steam at 80°C for 10 min, and then washed with clean water. Dry the washed cotton fiber until dry, and the drying temperature is 70°C.
[0043] After the anti-ultraviolet treatment of this embodiment, the long-staple cotton was spun and woven, and the ultraviolet protection factor (UPF) of the pure cotton fabric was tested to be 46.6.
PUM
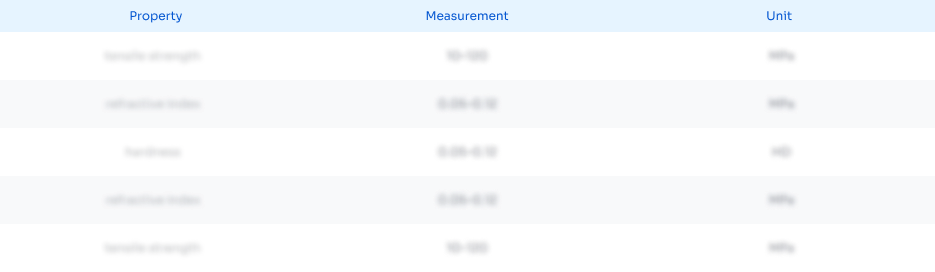
Abstract
Description
Claims
Application Information

- Generate Ideas
- Intellectual Property
- Life Sciences
- Materials
- Tech Scout
- Unparalleled Data Quality
- Higher Quality Content
- 60% Fewer Hallucinations
Browse by: Latest US Patents, China's latest patents, Technical Efficacy Thesaurus, Application Domain, Technology Topic, Popular Technical Reports.
© 2025 PatSnap. All rights reserved.Legal|Privacy policy|Modern Slavery Act Transparency Statement|Sitemap|About US| Contact US: help@patsnap.com