Inverse punching and blanking die
A punching blanking and flip-chip technology, which is applied in the field of stamping dies, can solve problems such as low production efficiency, many processes, and influence on product accuracy and quality, and achieve the goal of improving production efficiency, surface quality, and precision and quality. Effect
- Summary
- Abstract
- Description
- Claims
- Application Information
AI Technical Summary
Problems solved by technology
Method used
Image
Examples
Embodiment Construction
[0009] As an embodiment of the present invention, such as figure 1 As shown, a flip-chip punching and blanking die includes an upper die base 14, a lower die base 1, a handle 11, a guide sleeve 15 and a guide post 19, and the upper surface of the lower die base 1 is provided with a convex and concave die 17, and the convex and concave Die 17 has a punching hole, as preferably, the punching hole is a stepped hole with a small top and a big bottom, which is convenient for the discharge of waste materials. The convex and concave dies 17 are externally connected with a discharge plate 5, the discharge plate 5 is movably connected with the lower mold base 1 through the discharge screw 4, and a rubber pad 18 is arranged between the discharge plate 5 and the lower mold base 1. When the rubber pad 18 is in the During the uncompressed state, the upper surface of the stripping plate 5 is higher than the 2-3 workpiece material thickness on the convex and concave die 17 upper surfaces.
...
PUM
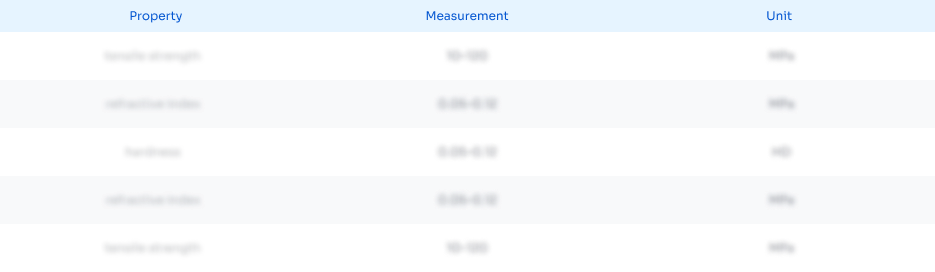
Abstract
Description
Claims
Application Information

- R&D Engineer
- R&D Manager
- IP Professional
- Industry Leading Data Capabilities
- Powerful AI technology
- Patent DNA Extraction
Browse by: Latest US Patents, China's latest patents, Technical Efficacy Thesaurus, Application Domain, Technology Topic, Popular Technical Reports.
© 2024 PatSnap. All rights reserved.Legal|Privacy policy|Modern Slavery Act Transparency Statement|Sitemap|About US| Contact US: help@patsnap.com