Tool path forming method based on curved surface morphology and curved surface dynamics of machined workpiece
A tool path and workpiece processing technology, which is applied in the field of computer-aided manufacturing, can solve problems affecting the performance of workpieces, and achieve the effects of improving service life, avoiding damage, and preventing cracks
- Summary
- Abstract
- Description
- Claims
- Application Information
AI Technical Summary
Problems solved by technology
Method used
Image
Examples
Embodiment Construction
[0022] Embodiments of the present invention will be further described in detail below in conjunction with the accompanying drawings.
[0023] like figure 1 As shown, a kind of tool path formation method based on machining workpiece curved surface topography and curved surface dynamics of the present invention, it comprises the following steps:
[0024] Step 1: If figure 2 As shown, taking the workpiece surface shape as the entry point, the force analysis of the workpiece working process is carried out, the workpiece solid model is established in the ANSYS software, and the six degrees of freedom of the lower surface of the workpiece are constrained, and the solid element Brick 8nbode 45 is selected for the workpiece solid model. Carry out mesh division, apply distributed force P on the upper surface of the solid model, apply uniform force F1 on the left surface of the solid model, and apply uniform force F2 on the right surface of the solid model, and obtain the force field ...
PUM
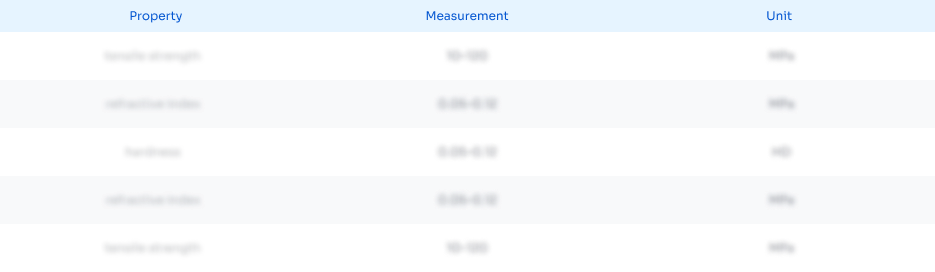
Abstract
Description
Claims
Application Information

- R&D
- Intellectual Property
- Life Sciences
- Materials
- Tech Scout
- Unparalleled Data Quality
- Higher Quality Content
- 60% Fewer Hallucinations
Browse by: Latest US Patents, China's latest patents, Technical Efficacy Thesaurus, Application Domain, Technology Topic, Popular Technical Reports.
© 2025 PatSnap. All rights reserved.Legal|Privacy policy|Modern Slavery Act Transparency Statement|Sitemap|About US| Contact US: help@patsnap.com