Method and device for intensity compensation of differential pressure sensor
A differential pressure sensor and intensity compensation technology, applied in measuring devices, instruments, measuring fluid pressure, etc., can solve the problems of complex sensor structure, unreliable performance, large volume and quality, etc., and achieve simple optical fiber layout and simplified data processing module , The effect of simplifying the overall optical path structure
- Summary
- Abstract
- Description
- Claims
- Application Information
AI Technical Summary
Problems solved by technology
Method used
Image
Examples
Embodiment Construction
[0046] The present invention will be further described in detail below in conjunction with the accompanying drawings and embodiments.
[0047] look first figure 1 , figure 1 The structural principle of the differential pressure sensor probe of the present invention is shown. As can be seen from the figure, the differential pressure sensor has two probes, namely probe one 11 and probe two 12. The structures of the two probes are exactly the same. In the probe housing 112 An elastic diaphragm 113 is arranged near the middle of the probe, and the elastic diaphragm 113 divides the interior of the probe housing 112 into two parts, one side is a detection cavity 111 and the other side is a fixing hole. The detection cavity 111 can allow the detection fluid to flow in, and the fixing hole can allow the optical fiber bundle 4 to be inserted. The optical fiber bundle 4 is processed into a bundle by 1 incident optical fiber 42 and 10 receiving optical fibers 41 (combined Figure 5 Th...
PUM
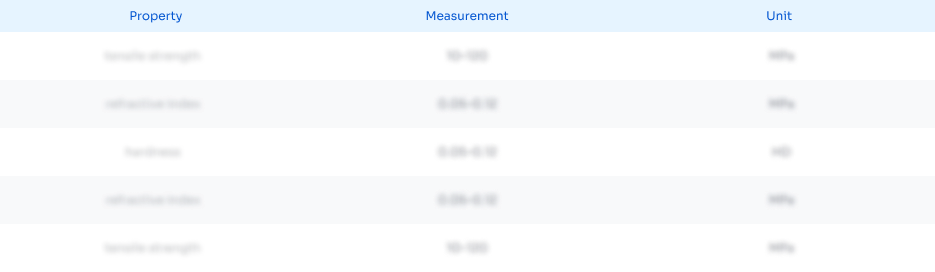
Abstract
Description
Claims
Application Information

- R&D
- Intellectual Property
- Life Sciences
- Materials
- Tech Scout
- Unparalleled Data Quality
- Higher Quality Content
- 60% Fewer Hallucinations
Browse by: Latest US Patents, China's latest patents, Technical Efficacy Thesaurus, Application Domain, Technology Topic, Popular Technical Reports.
© 2025 PatSnap. All rights reserved.Legal|Privacy policy|Modern Slavery Act Transparency Statement|Sitemap|About US| Contact US: help@patsnap.com