An oil pipe installation method for an iron bracket fuel sensor, its closing structure and the mold used
An installation method and sensor technology, applied in manufacturing tools, forming tools, metal processing and other directions, can solve the problems of difficult to ensure the accuracy of pipe position, waste of materials and man-hours, product quality decline, etc., to achieve good economic and social effects, convenient Manipulation, the effect of reducing the use of materials
- Summary
- Abstract
- Description
- Claims
- Application Information
AI Technical Summary
Problems solved by technology
Method used
Image
Examples
Embodiment Construction
[0016] The present invention will be further described below in conjunction with the accompanying drawings.
[0017] Such as figure 1 As shown, the main structure of the iron bracket fuel sensor includes a flange 1 and a fuel pipe 2. A metal plate punching hole 6 for the installation of the fuel pipe 2 is punched out on the flange 1. The diameter of the formed fuel pipe 2 is quite different from the diameter of the pipe. The diameters of the two ends of the oil pipe 2 are respectively: the small end 3 is Ф9.5+0.1 / -0.2mm, and the large end 4 is Ф10.98±0.15mm. At this time, the diameter of the punching hole 6 of the metal plate must be greater than Ф9.5, so Only the small end 3 can be loaded into the punching hole, and the conventional value is Ф9.7±0.1mm.
[0018] The oil pipe installation method of the iron bracket fuel sensor of the present invention is as follows: first punch out the punching hole 6 of the metal plate on the flange 1; then put the formed oil pipe 2 into the...
PUM
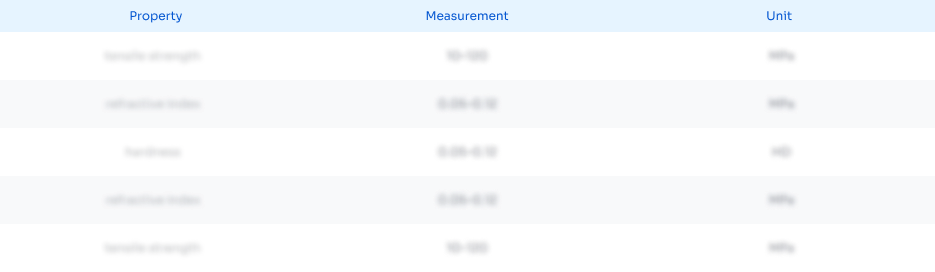
Abstract
Description
Claims
Application Information

- R&D
- Intellectual Property
- Life Sciences
- Materials
- Tech Scout
- Unparalleled Data Quality
- Higher Quality Content
- 60% Fewer Hallucinations
Browse by: Latest US Patents, China's latest patents, Technical Efficacy Thesaurus, Application Domain, Technology Topic, Popular Technical Reports.
© 2025 PatSnap. All rights reserved.Legal|Privacy policy|Modern Slavery Act Transparency Statement|Sitemap|About US| Contact US: help@patsnap.com