Welding method of magnet thin-walled cylinder body in sealed housing assembly
A technology of sealing shell and thin-walled cylinder, applied in welding equipment, electron beam welding equipment, metal processing equipment, etc. The effect of dense seam and easy operation
- Summary
- Abstract
- Description
- Claims
- Application Information
AI Technical Summary
Problems solved by technology
Method used
Image
Examples
Embodiment Construction
[0013] The present invention will be further illustrated in the following examples, which are only used to illustrate the present invention and not to limit the present invention.
[0014] see figure 1 . The sealed shell assembly has an aluminum alloy hollow thin shell shell 1, inside which is a cylindrical inner shell 2 that can be fixedly connected by electron beam I and electron beam II. The magnet 3 is assembled at the bottom end through the thin-walled cylinder inner casing 2 . The outer shell 1 with the inner shell 2 can seal the inner shell 2 and the magnet 3 in the hollow thin shell through the electron beam I and the electron beam II to form a sealed body. According to the pre-welding preparation of the present invention, conventional chemical methods can be used to remove the oxides on the joint surface of the sealing shell assembly, and an organic cleaning agent is used to strictly clean the vicinity of the joint to be welded before welding. Then use a special fi...
PUM
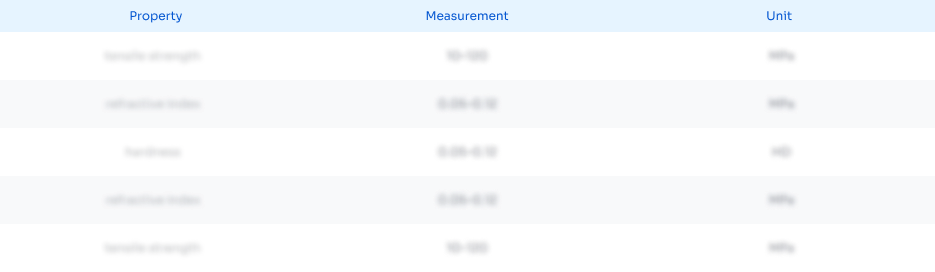
Abstract
Description
Claims
Application Information

- R&D
- Intellectual Property
- Life Sciences
- Materials
- Tech Scout
- Unparalleled Data Quality
- Higher Quality Content
- 60% Fewer Hallucinations
Browse by: Latest US Patents, China's latest patents, Technical Efficacy Thesaurus, Application Domain, Technology Topic, Popular Technical Reports.
© 2025 PatSnap. All rights reserved.Legal|Privacy policy|Modern Slavery Act Transparency Statement|Sitemap|About US| Contact US: help@patsnap.com