Cold rolling strip steel plate shape dynamic variable gain control method
A control method and strip-steel shape technology, applied in contour control and other directions, can solve the problems of difficult to obtain satisfactory control effect, unsatisfactory control effect, etc. awesome effect
- Summary
- Abstract
- Description
- Claims
- Application Information
AI Technical Summary
Problems solved by technology
Method used
Image
Examples
Embodiment
[0061] Step 1 Calculation of speed gain coefficient:
[0062] The speed gain is calculated, and the lag time is determined according to the trigger cycle of the shape measurement roller.
[0063] τ = l 2 πR
[0064] Values of control parameters: R is the radius of the shape measuring roll, which is 0.175m; l—the distance between the shape meter and the exit of the rolling mill, which is 4m.
[0065] The speed gain factor is:
[0066] kp _ v [ n ] = k _ fact [ n ] × t _ trig × t _ cycle t _ delay [ ...
PUM
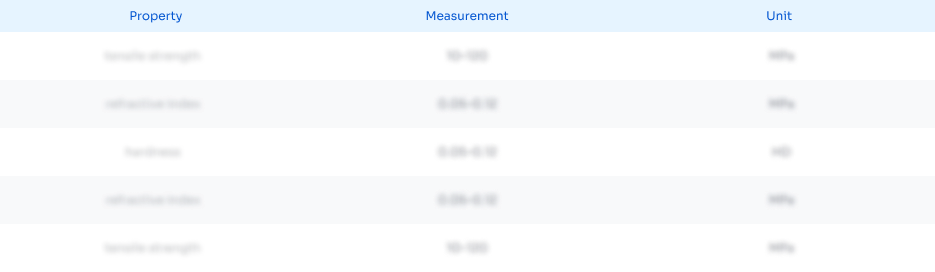
Abstract
Description
Claims
Application Information

- Generate Ideas
- Intellectual Property
- Life Sciences
- Materials
- Tech Scout
- Unparalleled Data Quality
- Higher Quality Content
- 60% Fewer Hallucinations
Browse by: Latest US Patents, China's latest patents, Technical Efficacy Thesaurus, Application Domain, Technology Topic, Popular Technical Reports.
© 2025 PatSnap. All rights reserved.Legal|Privacy policy|Modern Slavery Act Transparency Statement|Sitemap|About US| Contact US: help@patsnap.com