Method for preparing high purity rhodium trichloride by removing impurity from liquid phase digestion solution of waste rhodium catalyst
A technology of high-purity rhodium trichloride and rhodium catalyst is applied in the direction of improving process efficiency, can solve the problems of dilute concentration of the sample to be processed, high energy consumption for concentration, etc., and achieves the effects of mild process conditions, simple operation and easy industrialization.
- Summary
- Abstract
- Description
- Claims
- Application Information
AI Technical Summary
Problems solved by technology
Method used
Examples
Embodiment 1
[0021] The first step is to take the spent rhodium catalyst digestion solution (rhodium content 0.02 ~ 0.5wt%, other metal impurities are: sodium 10 ~ 15wt%, calcium 0.01 ~ 0.06wt%, iron 0.01 ~ 0.04wt%, nickel 0.001 ~ 0.004wt% %,) 30g, adjust the rhodium salt solution pH=1.5 with sodium hydroxide. 130 g of sodium oxalate solution with a mass concentration of 1% was added under stirring. The above mixture was stirred for 30 minutes and filtered to obtain a clear filtrate.
[0022] In the second step, dilute the filtrate 10 times with deionized water and heat it to a slight boiling state. Slowly add 1wt% sodium hydroxide solution dropwise to adjust the pH=8. Fully washed with water to obtain rhodium gel. Prepare 6 mol / L hydrochloric acid to dissolve the rhodium gel, then evaporate, concentrate and dry the obtained rhodium salt solution to obtain rhodium trichloride. Analysis and testing results show that the total amount of impurity elements in rhodium trichloride is 0.046%, ...
Embodiment 2
[0028] The operation process is the same as in Example 1, except that the pH is adjusted to 3.5 in the first step. The obtained rhodium trichloride analysis and detection results show that the total amount of impurity elements in rhodium trichloride is 0.039%, which meets the first-grade product quality index of YS / T593-2006. After calculation, the rhodium yield is 99.8%.
Embodiment 3
[0030] The operation process is the same as in Example 1, except that pH=5 is adjusted in the first step. The obtained rhodium trichloride analysis and detection results show that the total amount of impurity elements in rhodium trichloride is 0.042%, which meets the first-grade product quality index of YS / T593-2006. After calculation, the rhodium yield is 99.4%.
PUM
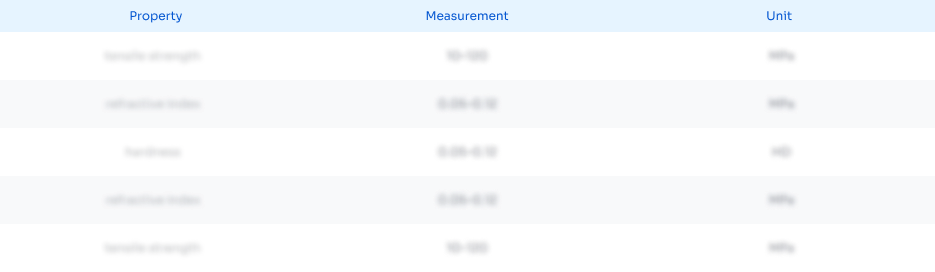
Abstract
Description
Claims
Application Information

- R&D
- Intellectual Property
- Life Sciences
- Materials
- Tech Scout
- Unparalleled Data Quality
- Higher Quality Content
- 60% Fewer Hallucinations
Browse by: Latest US Patents, China's latest patents, Technical Efficacy Thesaurus, Application Domain, Technology Topic, Popular Technical Reports.
© 2025 PatSnap. All rights reserved.Legal|Privacy policy|Modern Slavery Act Transparency Statement|Sitemap|About US| Contact US: help@patsnap.com